Custom Features That Can Increase Your RMC Plant Cost
- aimixglobal5
- Jul 3
- 4 min read
Investing in a Ready-Mix Concrete (RMC) plant is a major decision for any construction entrepreneur or company. Whether you are starting an rmc plant business or expanding an existing operation, understanding the factors that influence the overall cost of your plant is crucial. While the base price of a standard RMC plant might seem affordable, many buyers overlook the impact of custom features on the rmc plant cost.
Customizations can significantly improve your plant’s efficiency, productivity, and suitability for specific projects, but they also come with added expenses. In this article, we will explore some of the most common custom features that can increase your RMC plant cost and why choosing the right rmc plant manufacturer matters when planning your investment.

1. Automation and Control Systems
One of the first and most impactful customizations is the automation level in your RMC plant. While manual plants may be cheaper upfront, automated control systems bring greater accuracy, speed, and consistency.
PLC-based Control Systems: Programmable Logic Controllers (PLC) allow precise control over batching, mixing, and material handling. Higher-end systems integrate with remote monitoring and real-time data analytics.
SCADA Software: Supervisory Control and Data Acquisition software offers centralized control of the plant, enhanced troubleshooting, and data logging, which can optimize maintenance and reduce downtime.
Why it matters: Investing in automation can increase your plant cost by 15-30%, but it also boosts quality control and operational efficiency, essential for scaling your rmc plant business.
2. Capacity and Production Rate
RMC plants come in various capacities, typically measured in cubic meters per hour (m³/h). Customizing your plant to match your desired production volume is vital.
High-capacity Mixers: Larger mixers capable of producing 120 m³/h or more require robust components, increasing manufacturing costs.
Additional Bins and Hoppers: Increasing the number of aggregate bins allows storing more material types, enabling more complex mixes but adding to the plant’s footprint and cost.
Choosing a capacity that exceeds your immediate needs can raise initial costs but offers room for future growth.
3. Aggregate Handling and Storage
The design of the aggregate handling system directly affects operational ease and cost.
Conveyor Systems: Custom lengths or more conveyors to suit your site layout increase cost.
Aggregate Storage Silos: Larger or multiple silos improve storage capacity and reduce loading time, but add to structural and foundation costs.
Dust Collection Systems: To meet environmental regulations, many rmc plant manufacturers add dust suppression or collection equipment, which raises upfront expenses.
Customizing these features is important for plant efficiency and compliance but significantly affects your rmc plant cost.
4. Mixer Type and Configuration
The type of mixer you choose is a critical customization decision.
Twin-shaft Mixers: Known for fast, high-quality mixing, but usually more expensive.
Planetary Mixers: Provide thorough mixing, suited for specialty concrete, but add complexity and cost.
Drum Mixers: Typically less expensive, but slower and less consistent.
Your choice depends on the concrete types you plan to produce and production targets. Advanced mixers add both initial cost and maintenance requirements.
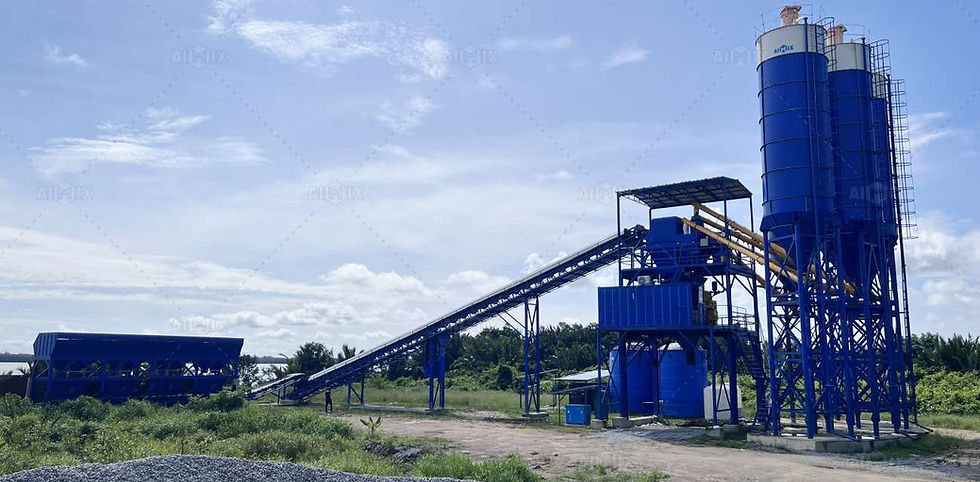
5. Water and Additive Systems
Modern RMC plants often include precise water dosing and admixture injection systems for better mix control.
Automated Water Meters: Ensure consistent water volume per batch, which enhances concrete quality.
Chemical Admixture Dosing Units: Support adding accelerators, retarders, plasticizers, and other additives automatically.
These systems improve mix quality and reduce waste but increase capital cost and require operator training.
6. Environmental and Safety Features
Compliance with local environmental laws and safety standards often requires custom modifications.
Noise Reduction Enclosures: Used to minimize sound pollution in urban areas.
Emission Control Systems: Filters and scrubbers to reduce dust and particulate matter.
Safety Guard Rails and Emergency Stop Systems: Enhanced safety features protect workers but add to equipment and installation costs.
These features are vital for legal compliance and corporate responsibility, though they add to the overall rmc plant cost.
7. Modular and Mobile Designs
If you plan to move your plant frequently or require rapid installation, modular or mobile plants are ideal but often cost more than fixed plants.
Mobile RMC Plants: Built on trailers or skids for easy transport and quick setup. They include compact systems but custom chassis or transport features add to cost.
Modular Plants: Pre-fabricated sections allow easier scalability but involve precision engineering and logistics expenses.
Choosing the right design depends on your business model and project locations in your rmc plant business plan.
8. Quality Control and Testing Facilities
Some rmc plant manufacturers offer custom laboratories or onsite testing equipment integrated into the plant design.
Concrete Testing Labs: To perform slump, compressive strength, and other quality tests.
Automatic Sampling Systems: Ensure representative sample collection.
Including these increases upfront investment but supports consistent product quality, a key competitive advantage.
9. Integration with Logistics and Delivery Systems
Optimizing the delivery process is another factor impacting cost.
Truck Loading Automation: Automated loading bays speed up dispatch and reduce labor.
Fleet Management Software: Tracks delivery trucks and concrete freshness, improving customer satisfaction.
This integration is often customized to client needs and adds software and hardware expenses.
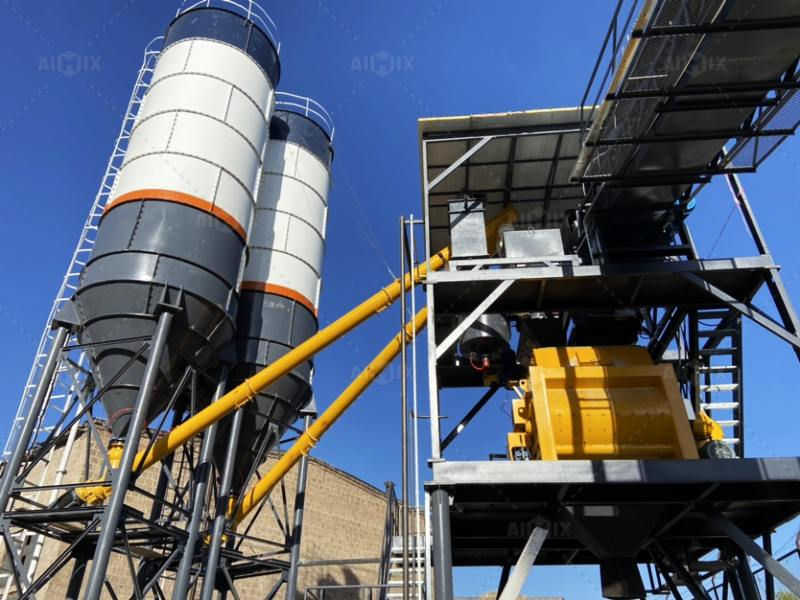
Choosing the Right RMC Plant Manufacturer
When planning your investment, selecting a reputable rmc plant manufacturer is as important as the features themselves. The right manufacturer will:
Help you balance custom features with your budget.
Provide reliable after-sales support and spare parts.
Assist in planning your rmc plant business with technical and operational guidance.
Ensure compliance with local standards and environmental regulations.
Working closely with experienced manufacturers can prevent costly over-specifications and streamline your purchase.
Conclusion
Custom features in an RMC plant can enhance performance, improve concrete quality, and provide a competitive edge in the market. However, these customizations come with increased initial and sometimes operational costs.
Whether you’re launching a new rmc plant business or upgrading an existing facility, understanding how different custom options affect your rmc plant cost is essential for budgeting and planning. Partnering with a knowledgeable rmc plant manufacturer ensures you select the right features that fit your production needs, site conditions, and financial constraints.
Careful planning, combined with smart customization, will set you up for a profitable and sustainable RMC operation.
Comments