Digital Control Systems for Mini Concrete Batching Plants: What’s New?
- aimixglobal5
- May 14
- 4 min read
In today’s fast-paced construction industry, efficiency, precision, and automation are no longer optional—they are essential. This is particularly true for compact equipment like the mini concrete batching plant, which is increasingly popular for urban projects, precast operations, and remote construction jobs. One of the most transformative developments in recent years is the rise of digital control systems designed specifically for these compact plants.
Whether you're investing in a mini mobile concrete batching plant or a stationary unit, modern control systems are redefining how these machines operate, improving everything from mix accuracy to overall productivity. Let’s explore what’s new in digital control systems and how these innovations are shaping the next generation of mini batching solutions.
Why Digital Control Systems Matter for Mini Plants
Traditionally, small concrete batching plants relied on manual or semi-automated controls. These systems often resulted in inconsistencies, human errors, and production delays. Today’s digital control systems offer significant improvements:
Precise mix control
Automatic calibration and weighing
Remote monitoring and diagnostics
Production data logging and reporting
User-friendly interfaces with touchscreen HMIs
These features are critical for ensuring consistent concrete quality, especially in a compact setup where batch size and accuracy must be tightly managed.
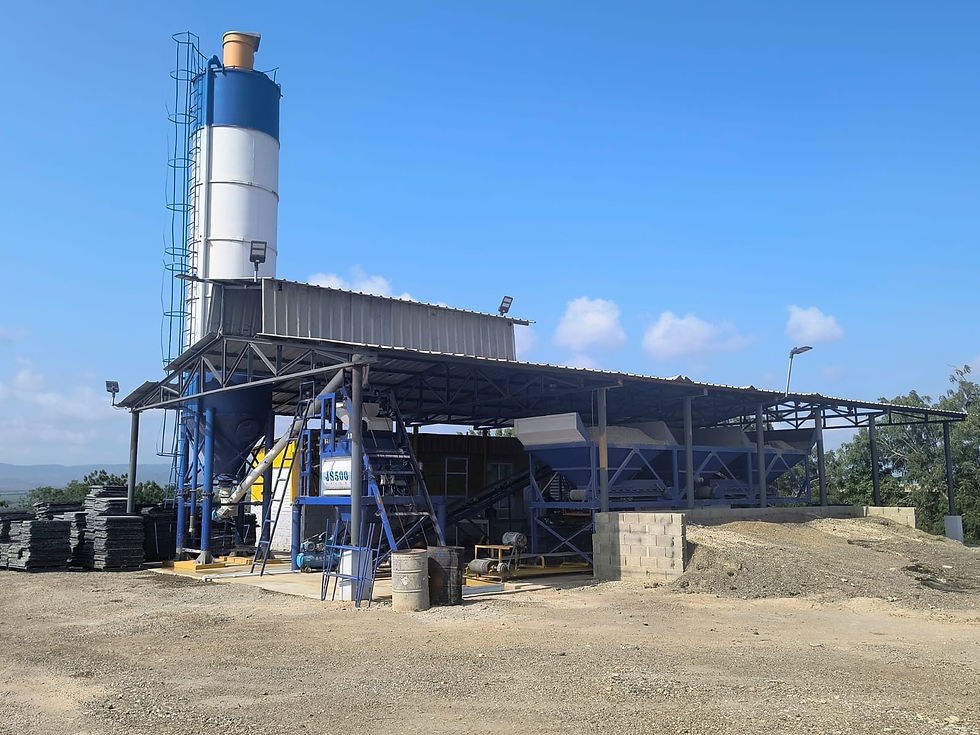
Key Features of Modern Control Systems
1. PLC-Based Automation
Programmable Logic Controllers (PLCs) are now standard in modern mini concrete batching plant systems. These industrial-grade computers offer:
High-speed data processing
Flexible programming logic
Real-time control of batching sequences
PLCs can manage everything from aggregate feeding and water dosing to cement weighing and discharge timing—all with minimal operator input.
2. Touchscreen Human-Machine Interfaces (HMIs)
Gone are the days of complicated switches and analog dials. Today’s mini batching plants feature large, colorful touchscreen HMIs. These interfaces allow operators to:
Select and store mix recipes
View live process data
Access troubleshooting guides
Adjust production parameters quickly
The simplicity of the interface makes it easier for teams to operate the plant with minimal training.
3. Automatic Material Weighing
Weighing accuracy is critical in producing high-quality concrete. Digital control systems now include automated weighing for:
Aggregates
Cement
Water
Admixtures
With load cell integration, the system continuously monitors material flow and adjusts in real time to stay within tolerance limits—an essential feature for mini mobile concrete batching plants that operate in diverse conditions.
4. Data Logging and Reporting
Modern digital systems provide extensive data management capabilities. Every batch is logged, including:
Mix design used
Actual weights of each component
Operator identity
Time and date stamps
These logs are useful for quality control, auditing, and customer reporting, and can also help identify production inefficiencies or material wastage.
5. Remote Monitoring and Diagnostics
Newer systems come with remote connectivity features, allowing supervisors and plant owners to:
Monitor plant performance from anywhere
Diagnose technical issues remotely
Update software or change mix designs without being onsite
This is especially beneficial for owners of mini mobile concrete batching plant deployed in remote locations, reducing the need for costly and time-consuming travel.

Benefits for Mobile and On-Site Applications
The mini mobile concrete batching plant segment has grown rapidly due to the demand for flexible, on-site mixing solutions. Digital control systems enhance mobile plant operations in several ways:
Faster setup and commissioning: The system can be preloaded with mix designs and startup protocols.
Better control in variable environments: Weather and job site conditions can affect concrete consistency; automation helps mitigate these risks.
Less dependency on skilled labor: Operators can quickly learn how to run the plant thanks to the intuitive digital interface.
With these advantages, contractors can deliver quality concrete wherever and whenever it’s needed, with consistent performance across all job sites.
Customization and Scalability
Digital control systems are now more modular and customizable. This means manufacturers can tailor systems to match specific project or business needs. Some customizable options include:
Multiple language support
Integration with accounting or logistics software
Real-time production dashboards
Automated alarms for maintenance or material shortages
These features make digital systems ideal not just for large commercial plants, but for small and mini concrete batching plant setups as well.
Future Trends: What’s Next?
The digital evolution of mini concrete batching plants is far from over. Future trends likely to shape the industry include:
AI-assisted mix optimization based on real-time material moisture and ambient conditions
Cloud-based fleet management for batching plants across multiple sites
Integration with mobile apps for instant mix order adjustments and live tracking
Voice-assisted controls for hands-free operation
As construction companies continue to adopt Industry 4.0 technologies, even small and mobile plants will benefit from high-tech solutions once reserved for large-scale industrial setups.

Conclusion
Digital control systems have completely changed the way mini concrete batching plants operate. By improving accuracy, efficiency, and ease of use, these systems offer unmatched value for contractors and plant owners alike. Whether you're managing a fixed facility or deploying a mini mobile concrete batching plant, adopting the latest digital technology is no longer optional—it’s a strategic necessity.
Investing in a digitally controlled mini plant ensures not just better concrete, but a better bottom line.
Comments