Hidden Costs That Influence Your RMC Plant Price
- aimixglobal5
- Apr 8
- 3 min read
When searching for a concrete batch plant for sale, many buyers focus primarily on the listed price of the equipment. While upfront costs are important, they rarely represent the full financial picture. In fact, several hidden costs—ranging from logistics and site preparation to maintenance and energy consumption—can significantly impact the true cost of owning and operating a ready-mix concrete (RMC) plant.
Understanding these hidden expenses is crucial for budgeting accurately, making smarter investment decisions, and ultimately improving your profit margins. This article uncovers the key hidden costs that often go overlooked when pricing an RMC plant.
1. Site Preparation and Infrastructure
One of the biggest overlooked expenses is site development. Even if you already own land, you'll need to invest in:
Ground leveling and compaction
Foundation construction for heavy equipment
Access roads and drainage
Utility connections (water, electricity, internet)
Depending on the terrain and location, site preparation can add 10–30% to your overall setup budget. If your chosen concrete batch plant for sale is high-capacity or includes a belt conveyor system, expect even more extensive groundwork.

2. Logistics and Transportation
Shipping your RMC plant components—especially large mixers, silos, and aggregate bins—can be costly.
Key logistics costs include:
Overseas freight charges
Customs duties and import taxes
Inland transportation to your site
Cranes and forklifts for unloading and installation
In some cases, shipping and handling can add up to 20% to your RMC plant price, especially if you're importing from a manufacturer located far from your project site.
3. Installation and Commissioning
Many buyers mistakenly believe that buying a concrete batch plant is a plug-and-play solution. In reality, installation requires skilled technicians and coordination of electrical, mechanical, and civil works.
Hidden installation costs may include:
Labor fees for installers and engineers
Local certification or inspection fees
Temporary utilities during setup
Testing and calibration of weighing systems and mixers
Unless these services are bundled in the sale contract, you'll need to budget separately for them.
4. Utility Consumption and Energy Efficiency
After your plant is installed, operational costs can start to build up—especially energy usage.
Common utility expenses:
Electricity for motors, mixers, conveyors, and controls
Diesel fuel (for generator-powered or mobile plants)
Water for mixing and washing
If your plant lacks energy-efficient components, your utility bills will rise over time. Even a small increase in power usage can translate to thousands in annual expenses.
Choosing an energy-optimized concrete batch plant for sale might cost more initially, but it can reduce operating costs in the long run.

5. Maintenance and Spare Parts
Routine maintenance is essential to keep your plant running smoothly. However, it's a cost many businesses don’t factor into their setup budget.
Hidden maintenance costs include:
Lubricants, filters, belts, and seals
Wear parts for mixers and conveyors
Software updates and control panel servicing
Emergency repairs due to downtime
Worse, if spare parts are not readily available, you may face delays and additional shipping charges. To reduce this risk, work with suppliers who offer local after-sales support or maintain warehouses in your region.
6. Operator Training and Staffing
Even the most advanced RMC plant can’t deliver profits if it’s operated by untrained personnel.
You’ll need to budget for:
On-site training provided by the manufacturer or a third-party expert
Operator salaries
Safety training and certifications
Inexperienced operators are more likely to cause mix errors, equipment damage, and safety issues—all of which increase your long-term costs.
7. Environmental Compliance
Most regions require environmental permits and dust or wastewater control systems to operate a ready mix plant legally.
Environmental-related hidden costs:
Dust collection systems and filters
Wastewater recycling and treatment units
Compliance documentation and audits
Noise suppression or fencing if located near residential areas
Failing to meet environmental standards can result in hefty fines or even forced shutdowns, so these costs must be considered from day one.
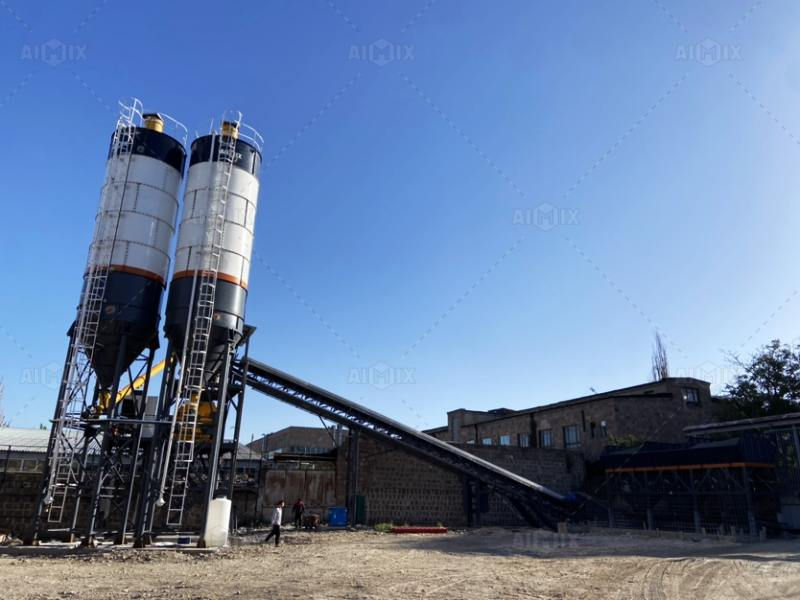
8. Customization and Upgrades
As your business grows, you might want to upgrade your RMC plant with:
Additional cement silos or admixture tanks
Automatic moisture sensors
Higher-capacity mixers or batching lines
These upgrades usually require modifications to the foundation, extra control software, and rewiring, all of which add unforeseen costs.
Purchasing a modular concrete batch plant for sale can help reduce these future upgrade expenses by making the system more flexible.
Final Thoughts
When evaluating the cost of an RMC plant, it’s important to look beyond the sticker price. From site preparation to operational inefficiencies, hidden costs can quickly inflate your budget and reduce your return on investment.
If you're considering a concrete batch plant for sale, take the time to:
Request a complete cost breakdown from the supplier
Ask about installation, training, and after-sales service
Plan for utilities, maintenance, and regulatory compliance
By making informed decisions upfront and choosing a plant that matches both your budget and long-term needs, you can maximize performance while protecting your bottom line.
Comments