How Land, Labor, and Regulations Affect Ready Mix Concrete Plant Cost
- aimixglobal5
- Jul 21
- 4 min read
Starting or expanding an rmc plant business involves many critical considerations beyond equipment and technology. Among the most influential factors that directly impact ready mix concrete plant cost are the costs associated with land acquisition, labor, and compliance with local regulations. For an rmc plant manufacturer, understanding how these variables fluctuate across different regions and project types is essential for providing accurate quotations and guiding clients toward cost-effective investments.
This article delves into how land, labor, and regulatory frameworks shape the overall cost of setting up and running a ready mix concrete (RMC) plant and how businesses can strategically manage these factors.
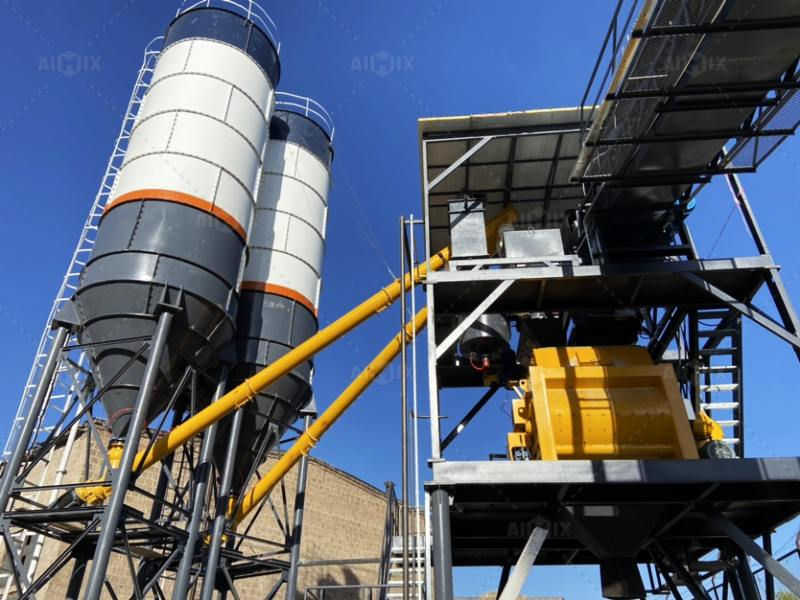
Land Costs: The Foundation of Your RMC Plant Investment
The price and availability of land is often the first major hurdle in establishing an rmc plant business. The ideal location balances proximity to raw materials, target markets, and transport infrastructure. However, land costs vary widely depending on urban density, industrial zoning, and regional demand.
Urban vs. Rural Land: Land in metropolitan or industrial zones commands a premium due to demand, convenience, and infrastructure access. For example, an rmc plant manufacturer operating near a major city may pay double or triple the land price compared to a rural site. This higher initial land investment directly raises the ready mix concrete plant cost.
Size and Layout Requirements: An efficient RMC plant needs sufficient space for storage silos, batching equipment, mixing areas, parking for delivery trucks, and possibly office facilities. Larger plots increase land expenses but may reduce operational inefficiencies. Careful site planning can optimize land use without inflating costs unnecessarily.
Zoning and Land Use Restrictions: Some areas may restrict industrial activity or impose buffer zones from residential neighborhoods, limiting where an RMC plant can be situated. These restrictions might force a plant to locate farther from markets, increasing logistics costs.
Labor Costs: Skilled Workforce and Operational Efficiency
Labor expenses form a significant portion of the ongoing operational costs in an rmc plant business. The complexity of RMC plant operations demands skilled workers who can operate batching machinery, maintain equipment, manage quality control, and handle logistics.
Local Wage Rates: Labor costs vary widely by region, influenced by the local economy, labor laws, and skill availability. An rmc plant manufacturer in countries with high minimum wages or unionized labor will face steeper payroll expenses, increasing the overall ready mix concrete plant cost.
Training and Skill Level: Investing in a well-trained workforce reduces errors, improves plant efficiency, and lowers maintenance costs. While initial training adds to labor expenses, it often results in long-term savings and higher quality output.
Labor Availability: In some regions, skilled labor shortages may drive up wages or force companies to import workers, adding recruitment and compliance costs. Conversely, areas with abundant labor may offer competitive wage rates but require investment in training to ensure quality.
Automation and Labor Reduction: Many modern RMC plants incorporate automation to reduce labor dependency. While this can increase the plant’s upfront cost, it lowers long-term labor expenses and mitigates risks associated with labor shortages.

Regulations: Navigating Compliance and Its Impact on Costs
Compliance with local, regional, and national regulations can significantly affect ready mix concrete plant cost. Regulations influence everything from plant design and emissions control to worker safety and waste management.
Environmental Regulations: RMC plants often face strict environmental standards to control dust, noise, water runoff, and air emissions. Complying may require investing in dust collection systems, water recycling units, and noise barriers, all adding to capital expenditure.
Permitting and Licensing: Obtaining permits for construction and operation can be time-consuming and expensive. Fees, environmental impact assessments, and required modifications to plant design can delay projects and increase costs.
Health and Safety Standards: Meeting occupational health and safety requirements often necessitates additional investments in safety equipment, training programs, and facility design adaptations. Non-compliance risks fines and shutdowns, making proactive compliance a cost-saving strategy.
Building Codes and Zoning Laws: Regulations may impose restrictions on building heights, setbacks, or operational hours, influencing plant layout and productivity.
Sustainability and Carbon Reporting: With increasing focus on green building and carbon footprint reduction, some regions require emissions reporting and adherence to sustainability standards, potentially increasing operational costs.
Strategic Considerations for RMC Plant Manufacturers and Business Owners
An experienced rmc plant manufacturer can guide clients in navigating the complexities of land, labor, and regulatory impacts on plant cost by offering tailored solutions.
Site Selection Support: Advising on optimal plant location based on cost, logistics, and regulatory environment minimizes unforeseen expenses.
Customized Plant Design: Designing modular or compact plants to fit constrained land parcels or meet specific regulatory requirements reduces wasted capital.
Labor Training Programs: Providing or recommending comprehensive operator training ensures high productivity and compliance with safety standards.
Automation Integration: Balancing automation to reduce labor costs without excessive capital outlay optimizes both upfront and operating expenses.
Compliance Consulting: Helping businesses understand local laws and manage permitting accelerates project timelines and avoids costly penalties.
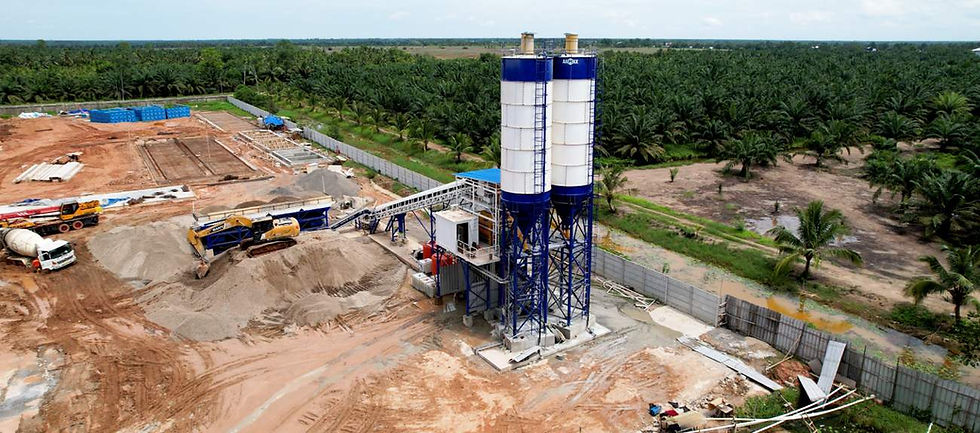
Conclusion
Land, labor, and regulations are three pillars that heavily influence ready mix concrete plant cost and operational viability. For those in the rmc plant business, effectively managing these factors is crucial to launching a profitable and sustainable operation. Working closely with a knowledgeable rmc plant manufacturer who understands regional nuances can lead to smarter investments, smoother project delivery, and long-term success.
If you’re planning to set up or expand your RMC plant, consider these critical factors early in your budgeting and planning phases to avoid surprises and optimize your capital and operational expenditure.
Comments