How to Fix Blockage of Mini Concrete Pumps for Sale
- aimixglobal5
- Apr 28
- 3 min read
Mini concrete pumps are essential machines in construction projects, allowing for efficient and precise concrete placement. However, blockages are a common issue that can disrupt workflow and damage the equipment if not addressed properly. In this guide, we will explore the causes of blockages in mini concrete pumps for sale, preventive measures, and step-by-step solutions to fix them effectively.
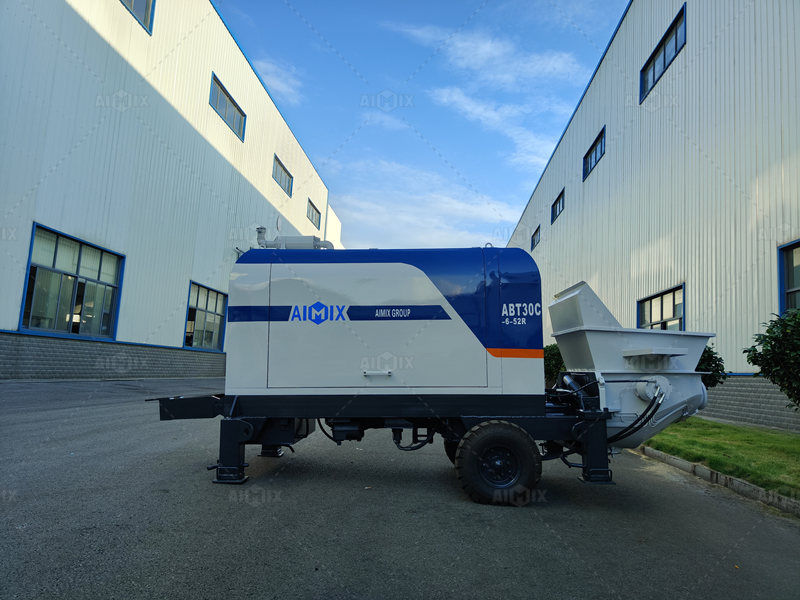
Common Causes of Blockages in Mini Concrete Pumps
Understanding why blockages occur is the first step in preventing and resolving them. Some of the most frequent causes include:
1. Poor Concrete Mix Design
If the concrete mix is too dry or lacks proper slump, it can cause resistance in the pipeline.
Excessively thick or sticky mixes increase friction, leading to blockages.
Large aggregates or irregularly shaped stones can get stuck in the pipeline.
2. Incorrect Pipeline Setup
Sharp bends or too many elbows in the pipeline increase the risk of blockages.
Using pipes with inconsistent diameters can disrupt the flow of concrete.
Poorly lubricated pipes before pumping can cause material buildup.
3. Pumping Technique Errors
Interruptions in pumping can allow concrete to settle and harden inside the pipes.
Running the pump at too high or too low pressure can lead to inconsistent flow.
Failure to clean the pump properly after use can leave residue that hardens over time.
4. Mechanical Issues
Worn-out seals or pistons can reduce pumping efficiency.
Air leaks in the system can disrupt the suction process.
Faulty valves or hydraulic issues may prevent smooth concrete flow.
Preventive Measures to Avoid Blockages
Prevention is always better than cure. Here are some best practices to minimize the risk of blockages in mini concrete pumps:
1. Optimize the Concrete Mix
Ensure the concrete has a suitable slump (typically between 4-6 inches for pumping).
Use well-graded aggregates to prevent segregation.
Avoid overly stiff or excessively wet mixes.
2. Proper Pipeline Setup
Use smooth, high-quality pipes with minimal bends.
Ensure all connections are tight and secure to prevent leaks.
Lubricate the pipeline with a cement slurry or pumping aid before starting.
3. Correct Pumping Techniques
Maintain a steady pumping speed to avoid sudden pressure changes.
Avoid long pauses; if stopping is necessary, reverse the pump briefly to relieve pressure.
Clean the pump and pipes thoroughly after each use.
4. Regular Maintenance
Inspect seals, pistons, and valves for wear and tear.
Check hydraulic oil levels and ensure no air is trapped in the system.
Replace damaged or worn-out parts promptly.
Step-by-Step Guide to Fixing a Blockage
If a blockage occurs, follow these steps to clear it safely and efficiently:
Step 1: Identify the Blockage Location
Listen for unusual noises or pressure spikes in the pump.
Check the pipeline section by section to locate the clog.
Step 2: Reverse Pumping (If Possible)
Many mini concrete pumps have a reverse function. Engage it to dislodge the blockage.
If successful, resume normal pumping slowly.
Step 3: Disassemble the Pipeline
If reversing doesn’t work, shut off the pump and release pressure.
Disconnect the pipes starting from the farthest point from the pump.
Use a high-pressure water jet or a rubber plunger to push out the clog.
Step 4: Remove Hardened Concrete
If the blockage has hardened, use a hammer and chisel (carefully) to break it apart.
Alternatively, specialized cleaning balls or foam plugs can help clear residue.
Step 5: Reassemble and Test
Reconnect all pipes securely.
Run water or a cleaning agent through the system to ensure smooth flow.
Resume pumping with a properly mixed batch of concrete.
When to Seek Professional Help
If the blockage persists despite troubleshooting, it may indicate a deeper mechanical issue, such as:
Severe wear in the pumping cylinders
Hydraulic system malfunctions
Valve or seal failures
In such cases, contact a technician or the manufacturer of your mini concrete pump for professional servicing.
Blockages in mini concrete pumps for sale can be frustrating, but with proper knowledge and preventive measures, they can be minimized. By optimizing the concrete mix, maintaining the equipment, and following correct pumping techniques, most blockages can be avoided. If a clog does occur, acting quickly with the right steps will restore your pump’s functionality and keep your project on track.
Regular maintenance and proper handling are key to ensuring the longevity and efficiency of your concrete pumping machine. Investing time in prevention will save you costly repairs and downtime in the long run.
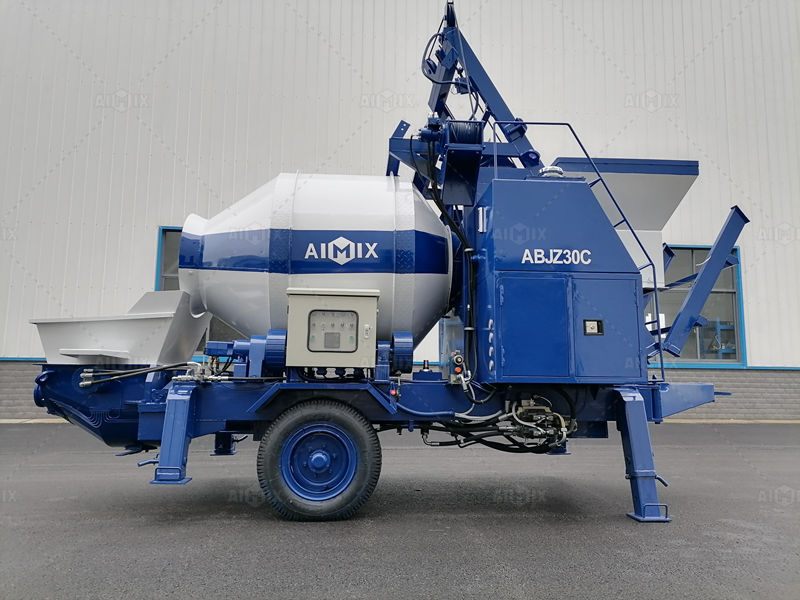
Comments