How to Minimize RMC Plant Cost through Smart Operations and Maintenance
- aimixglobal5
- Mar 2
- 5 min read
The cost of running a Ready Mix Concrete (RMC) plant is a significant factor for businesses in the construction and manufacturing industries. Whether it's a mobile batching plant or a stationary concrete batching plant, optimizing operational efficiency and minimizing maintenance costs are crucial for maximizing profits. In this article, we will explore strategies that can help businesses reduce RMC plant costs, focusing on smart operations and maintenance practices, as well as how to manage costs related to mobile batching plant price and stationary concrete batching plant price.

The Importance of Smart Operations in RMC Plants
Efficient operations are the backbone of a successful RMC plant. To minimize costs, plant managers must focus on optimizing the production process and ensuring that all resources, such as raw materials and labor, are used effectively. Below are several strategies to optimize operations:
1. Optimizing Material Usage
One of the largest expenses in an RMC plant is the cost of raw materials like cement, aggregates, and water. By accurately measuring and mixing the right amounts of these materials, plant managers can reduce waste and lower costs. Implementing automated systems that provide real-time data on material consumption can significantly improve the accuracy of batching, preventing overuse of expensive raw materials.
Additionally, maintaining good relationships with suppliers can help ensure that the plant gets high-quality materials at competitive prices. Regularly assessing and negotiating contracts with material suppliers can result in lower material costs.
2. Efficient Mixing Process
The efficiency of the mixing process directly impacts both product quality and energy consumption. A well-calibrated batching system ensures that the concrete mix is consistently accurate, which improves both the quality of the concrete and the production rate. By reducing the need for rework or adjustments due to incorrect batching, businesses can minimize operational disruptions and ensure that every batch meets the required specifications.
Using energy-efficient mixing equipment can also reduce the overall energy consumption of the plant. For example, high-efficiency motors, improved insulation, and optimized mixing times can cut down on electricity costs, which can add up significantly over time.
3. Smart Scheduling and Production Planning
Production scheduling plays a vital role in minimizing the operating costs of an RMC plant. By analyzing historical data and forecasting future demand, plant managers can plan production schedules that optimize plant capacity and reduce idle time. Effective scheduling can also help in minimizing overtime costs and improving plant throughput.
Furthermore, it’s essential to account for peak demand periods and align plant operations with customer requirements. By streamlining production scheduling, plants can avoid overproduction, which can lead to excess inventory costs or underproduction, which might affect project deadlines.
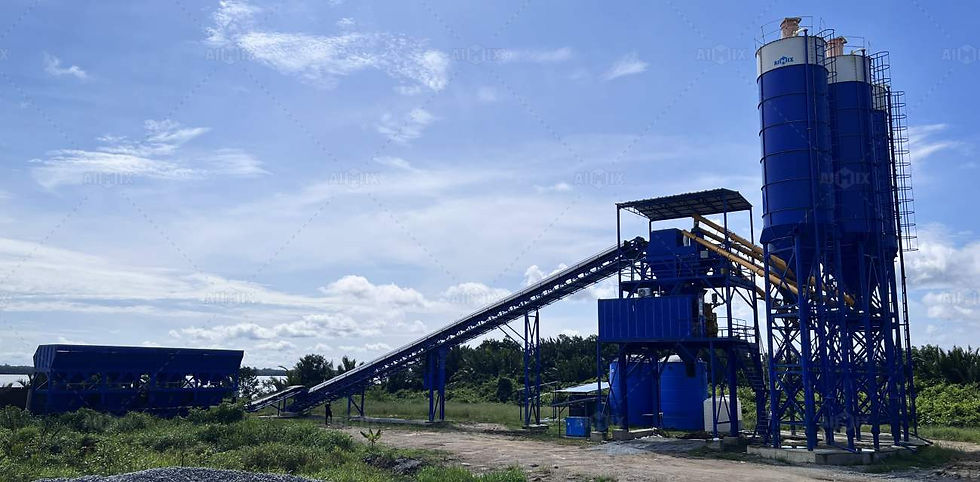
Minimizing Maintenance Costs with Preventive Strategies
Maintenance costs are another major area where RMC plants can save money. Regular maintenance not only ensures the longevity of the equipment but also improves plant efficiency by reducing downtime. The following preventive maintenance strategies can minimize operational costs:
1. Regular Equipment Inspections and Upkeep
Routine inspections are crucial for identifying potential problems before they escalate. Common maintenance tasks for RMC plants include checking and calibrating batching equipment, inspecting mixing drums, and ensuring that all mechanical components are properly lubricated. By staying ahead of wear and tear, businesses can prevent costly breakdowns that may lead to expensive repairs and extended downtime.
Implementing a digital maintenance management system that tracks equipment performance and maintenance history can help plant operators stay on top of necessary inspections and repairs. This proactive approach reduces the risk of equipment failure and ensures that the plant runs smoothly.
2. Investing in High-Quality Equipment
While high-quality equipment might require a larger initial investment, it can pay off in the long run by reducing maintenance costs and extending the equipment's lifespan. Whether it’s a mobile batching plant or a stationary concrete batching plant, investing in durable machinery means fewer repairs and replacements over time. Additionally, high-quality equipment often offers better energy efficiency, which contributes to lowering operating costs.
For example, mobile batching plants, known for their mobility and versatility, often feature advanced technologies that optimize the batching and mixing process, reducing wear and tear. Stationary plants, with their robust construction, are designed for high-volume production and can withstand the stresses of continuous operation. Both types of plants, when chosen carefully, can provide significant cost savings over time.
3. Train Employees on Proper Equipment Handling
Proper training is essential to ensure that plant employees can operate equipment safely and efficiently. Misuse or improper handling of equipment can lead to damage, which will incur high repair costs. Regular training programs focusing on operational best practices and safety protocols can improve the plant’s overall performance and reduce human error.
Employees should be trained to recognize the importance of maintaining proper batch sizes, operating equipment at optimal speeds, and adhering to recommended maintenance schedules. Regular refresher courses can help keep everyone on the same page, preventing costly mistakes.
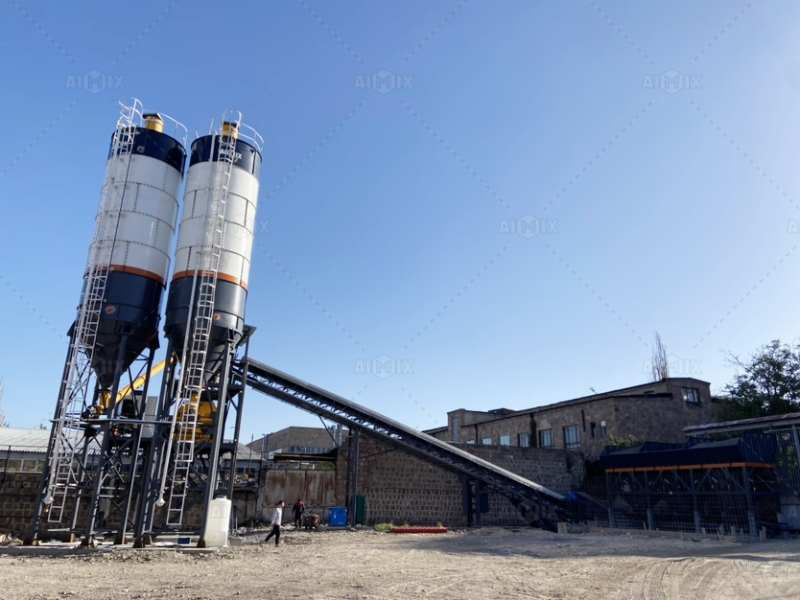
Cost Considerations: Mobile vs. Stationary Concrete Batching Plants
When considering the cost of an RMC plant, it's important to evaluate the specific needs of your business, including whether a mobile batching plant or a stationary concrete batching plant is the best option. Each type has its advantages and impacts the overall cost structure differently.
Mobile Batching Plant Price
Mobile batching plants are typically more cost-effective in terms of initial investment when compared to stationary plants. The mobile batching plant price depends on factors such as production capacity, features, and automation. These plants are designed for flexibility and portability, making them ideal for businesses that require concrete production on multiple job sites.
However, the operational costs of a mobile batching plant can be higher than that of a stationary plant due to increased transportation and setup time. The plant’s capacity is usually smaller, and frequent moving may lead to higher maintenance costs. On the other hand, if your projects involve various locations or short-term projects, mobile batching plants can save costs by reducing the need for additional infrastructure.
Stationary Concrete Batching Plant Price
Stationary concrete batching plants are generally larger, more stable, and designed for high-volume, continuous operations. While the initial investment in a stationary plant may be higher than that of a mobile plant, they offer greater economies of scale for large projects. These plants have higher production capacities and are more efficient for large-scale projects, helping to minimize per-unit production costs over time.
For businesses that require long-term, consistent concrete production, a stationary plant can be the more cost-effective option in the long run, especially when considering lower transportation and setup costs. Additionally, stationary plants tend to be less costly to maintain due to their fixed nature and larger, more robust components.
Conclusion
Minimizing RMC plant costs requires a combination of smart operations, efficient maintenance, and selecting the right equipment. By optimizing material usage, improving mixing processes, and implementing preventive maintenance strategies, plant managers can significantly reduce operational expenses. Additionally, understanding the differences between mobile batching plant price and stationary concrete batching plant price allows businesses to make more informed decisions about which type of plant best suits their needs. With careful planning and investment, businesses can maintain competitive advantage, increase efficiency, and achieve long-term savings.
Comments