Innovations by Concrete Batching Plant Manufacturers to Boost Production Quality
- aimixglobal5
- Mar 3
- 5 min read
Concrete batching plants play a vital role in the construction industry by providing high-quality concrete for a variety of projects, including residential buildings, highways, bridges, and industrial structures. With the increasing demand for faster, more efficient, and higher-quality production, concrete batching plant manufacturers have continuously innovated to meet the evolving needs of the market. These innovations have led to improvements in efficiency, sustainability, precision, and automation, resulting in superior concrete quality and optimized production processes.
As the construction industry moves toward more complex and larger-scale projects, the role of manufacturers in driving innovation in concrete batching plants becomes even more critical. This article will explore some of the key innovations made by concrete batching plant manufacturers that are boosting production quality, with a focus on ready mix concrete plants for sale and stationary concrete batch plants for sale.
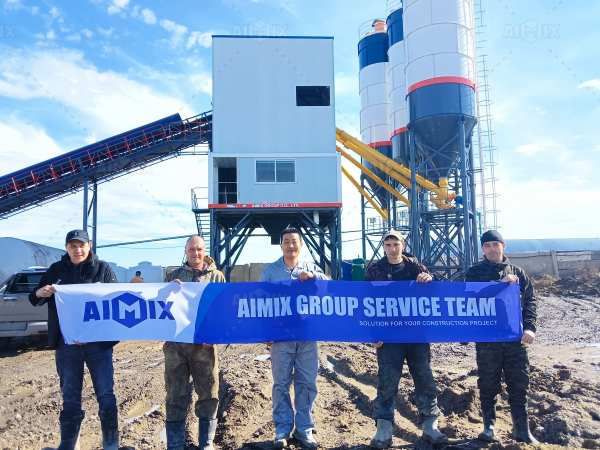
1. Automation and Digital Integration
One of the most significant innovations in recent years has been the integration of automation and digital technology into concrete batching plants. These technologies are designed to streamline the mixing process, improve accuracy, and reduce human error, leading to higher-quality concrete production.
Automated Control Systems: Modern concrete batching plants now feature automated control systems that allow for precise adjustments in the mix design, ensuring the consistency and quality of the final product. These systems can monitor and control every aspect of the batching process, from ingredient input to mixing time, water addition, and output. Automated systems also help optimize the production process, reducing the need for manual labor and minimizing the risk of errors.
Digital Monitoring and Reporting: Digital systems now allow for real-time monitoring of batching plant operations, ensuring that everything is running smoothly. Plant managers can track production data, such as concrete strength, mix proportions, and environmental conditions, which is vital for maintaining quality standards. Many modern batching plants are equipped with cloud-based software that allows managers to access production data remotely, enabling quicker decision-making and minimizing downtime.
Integration with Other Technologies: Some batching plant manufacturers have integrated their plants with technologies like GPS tracking, inventory management, and supply chain systems to optimize the overall production process. These systems improve efficiency and help maintain a consistent quality of concrete, whether for a ready mix concrete plant for sale or a stationary concrete batch plant for sale.
2. Improved Mixing Technology
The mixing process is one of the most critical stages in concrete production. Innovations in mixing technology have resulted in better quality control and consistency, ensuring that the final product meets or exceeds industry standards.
Advanced Mixing Techniques: Newer models of concrete batching plants are equipped with high-performance mixers designed to deliver a more homogeneous mix. These mixers ensure that all components, including aggregates, cement, and water, are evenly distributed, resulting in a higher-quality concrete mixture. Advanced mixing technology, such as twin-shaft mixers and planetary mixers, provides faster and more efficient mixing, ensuring the uniformity of the concrete produced.
Smart Mixing Control: Some batching plant manufacturers have incorporated smart mixing control systems that automatically adjust the speed and time of mixing based on the specific material characteristics. This ensures that each batch of concrete meets the desired strength and consistency requirements. These intelligent systems also minimize waste by preventing over-mixing or under-mixing, which can compromise the quality of the concrete.
Energy Efficiency: Innovations in energy-efficient mixing equipment have reduced the energy consumption of concrete batching plants, lowering operating costs while maintaining high production quality. By using more efficient motors and reducing the time required for mixing, these plants are able to produce higher-quality concrete without unnecessary energy expenditure.
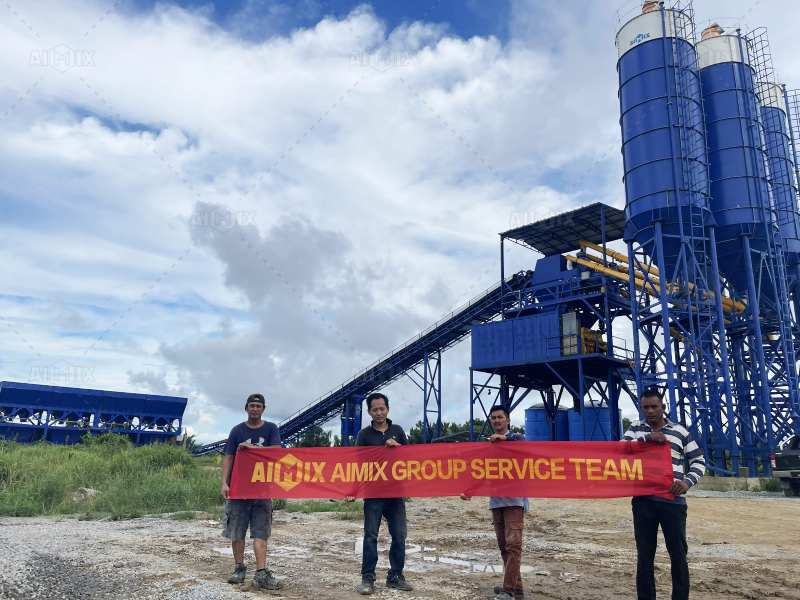
3. Improved Material Handling and Storage
The quality of concrete is heavily dependent on the raw materials used in its production. Innovations in material handling and storage have enabled concrete batching plants to use a wider variety of high-quality raw materials, resulting in stronger and more durable concrete.
Precise Material Measurement: Manufacturers have developed more accurate systems for measuring and delivering raw materials to the mixer. With highly accurate weighing scales and automated feed systems, concrete batching plants can ensure that the correct proportions of cement, aggregates, and water are used in each batch, maintaining the desired strength and consistency.
Efficient Aggregate Storage: Storage innovations, such as silo systems and covered aggregate storage units, have improved the handling and preservation of raw materials. These systems protect aggregates from contamination, ensuring that the materials remain dry and free of impurities that could negatively affect the concrete's quality.
Recycling and Waste Management: Many modern concrete batching plants are designed to handle and recycle waste material efficiently. Concrete batch plants now feature systems that can recycle leftover concrete, reintroducing it into the mixing process. This not only reduces waste but also helps conserve resources, making the production process more sustainable.
4. Sustainability and Eco-Friendly Practices
Sustainability has become a top priority for many industries, and the concrete batching plant sector is no exception. Manufacturers are increasingly adopting eco-friendly practices and technologies to reduce the environmental impact of concrete production while maintaining high production quality.
Water Recycling Systems: One of the significant environmental impacts of concrete batching plants is water usage. To mitigate this, many manufacturers have developed closed-loop water recycling systems that allow plants to reuse water in the mixing process. This innovation reduces the plant's water consumption and ensures that wastewater is treated and safely disposed of, improving the environmental footprint of the plant.
Reduced Carbon Footprint: Concrete production is a major contributor to CO2 emissions, primarily due to cement production. Some concrete batching plant manufacturers have adopted technologies that reduce the carbon footprint of the production process, such as using alternative materials (like fly ash and slag) to replace part of the cement content. These materials can reduce the amount of cement needed and lower the plant’s overall CO2 emissions.
Energy-Efficient Operations: To further minimize environmental impact, many plants are investing in energy-efficient equipment and renewable energy sources. Solar panels, energy-efficient motors, and hybrid diesel-electric systems are becoming more common in new batching plants, helping to reduce the plant's energy consumption and carbon footprint.
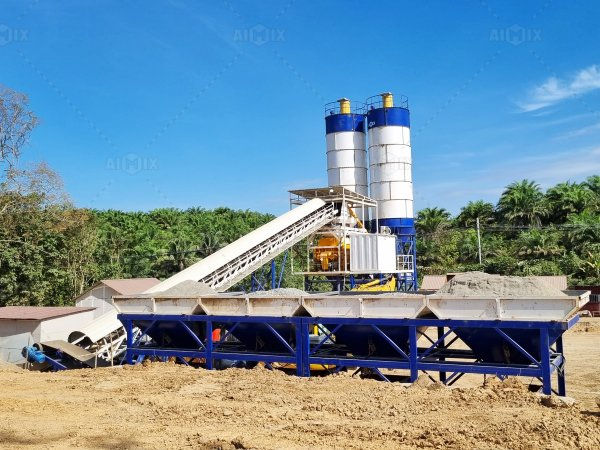
5. Ready Mix Concrete Plant for Sale vs. Stationary Concrete Batch Plant for Sale
When considering innovations, it’s important to understand the differences between the two main types of concrete batching plants available for sale: ready mix concrete plants and stationary concrete batch plants.
Ready Mix Concrete Plant for Sale: Ready mix concrete plants are designed to produce concrete in bulk and deliver it to construction sites where it’s needed. They are typically highly automated, with advanced mixing, measurement, and delivery systems. Innovations in ready mix plants focus on optimizing the logistics of concrete delivery, improving delivery times, and maintaining the consistency and quality of the concrete until it reaches the job site.
Stationary Concrete Batch Plant for Sale: Stationary concrete batch plants are designed for large-scale, long-term production and are typically located at construction sites or in industrial areas. Innovations in stationary plants focus on enhancing the plant’s durability, maximizing production efficiency, and improving the quality of the concrete produced over extended periods. These plants are often used for projects requiring consistent, high-quality concrete production.
Conclusion
Innovations by concrete batching plant manufacturers have revolutionized the industry, leading to significant improvements in the quality and efficiency of concrete production. Automation, digital integration, advanced mixing technology, and eco-friendly practices have all played a part in improving production quality. Whether you’re considering a ready mix concrete plant for sale or a stationary concrete batch plant for sale, these innovations ensure that modern batching plants are more efficient, sustainable, and capable of delivering high-quality concrete for a variety of construction projects. By staying at the forefront of technological advancements, concrete batching plant manufacturers continue to shape the future of the construction industry.
Comments