Innovative Technologies in Concrete Mixer Plants: Enhancing Performance and Sustainability
- aimixglobal5
- Jan 19
- 4 min read
In the construction industry, the quality of concrete is a crucial factor in the success of any project. Concrete mixer plants, particularly ready mix concrete batch plants, play a pivotal role in ensuring that concrete production meets the required standards. The increasing demand for higher performance and sustainability in the construction sector has led to significant technological advancements in concrete mixer plants. These innovations not only enhance the efficiency and reliability of concrete production but also contribute to reducing environmental impact.
1. Automation and Control Systems
One of the most significant innovations in modern concrete mixer plants is the integration of advanced automation and control systems. These systems allow for precise control over the mixing process, ensuring consistent quality and reducing the chances of human error. The automation in ready mix concrete batch plants extends to the monitoring of material proportions, mixing time, and discharge procedures. As a result, batch plant operators can achieve high accuracy and minimize wastage.
Additionally, these systems improve operational efficiency by reducing downtime and optimizing the production schedule. The ability to remotely monitor and control operations from a centralized location also allows for real-time adjustments, ensuring that concrete is mixed to the desired specifications every time. Many concrete batch plant manufacturers are now incorporating advanced software that provides detailed reports on each batch, which enhances traceability and quality assurance.
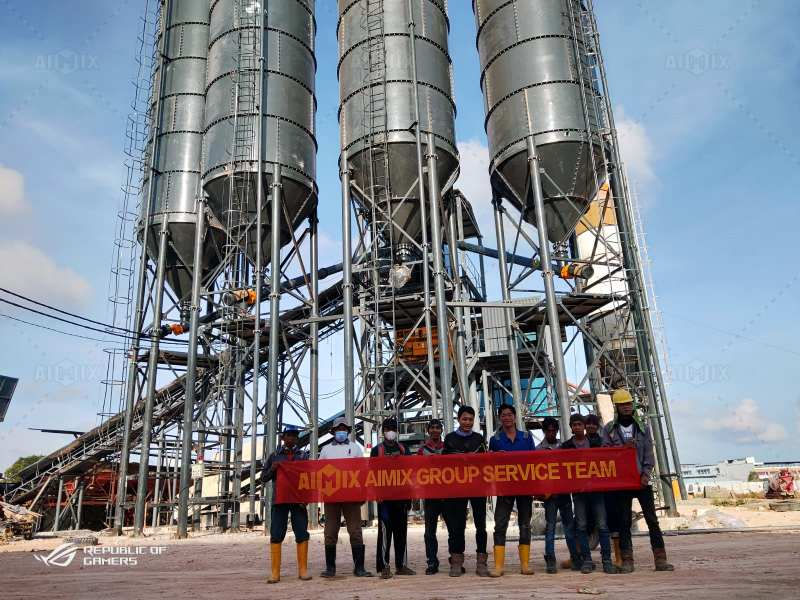
2. Environmental Sustainability
As sustainability becomes a top priority in the construction industry, concrete mixer plants are evolving to meet environmental standards. Traditional concrete production is resource-intensive, consuming large amounts of water and energy while contributing to greenhouse gas emissions. However, with the introduction of new technologies, concrete mixer plants are becoming more environmentally friendly.
Recycling systems are one of the most notable innovations. Ready mix concrete batch plants now incorporate systems that allow for the reuse of water and aggregates. This not only reduces waste but also conserves valuable resources. The water used in the concrete mixing process can be collected, filtered, and reused for subsequent batches, reducing the demand for fresh water. Furthermore, the recycling of aggregates minimizes the environmental impact associated with quarrying and transportation of raw materials.
Another innovation is the use of energy-efficient motors and drives in concrete mixer plants. These components reduce electricity consumption, which is a major cost factor in concrete production. Solar panels and other renewable energy sources are also being integrated into plant operations to reduce reliance on fossil fuels and lower the carbon footprint of the production process.
3. Mobile and Modular Concrete Mixer Plants
The demand for flexibility and faster deployment in the construction industry has led to the rise of mobile and modular concrete mixer plants. Mobile plants are designed for easy transportation and setup at construction sites, making them ideal for projects that require on-site concrete production. These plants can be quickly assembled and dismantled, offering a cost-effective solution for projects with limited timeframes or locations that are difficult to access.
Modular plants, on the other hand, offer the flexibility to expand or modify the plant as the project requirements change. The modular design allows for easy upgrades, such as adding more mixers or improving storage capacity. This adaptability makes modular concrete mixer plants a versatile choice for contractors who need scalable solutions. Many concrete batch plant manufacturers are focusing on providing these mobile and modular options to cater to the growing demand for flexibility in the industry.
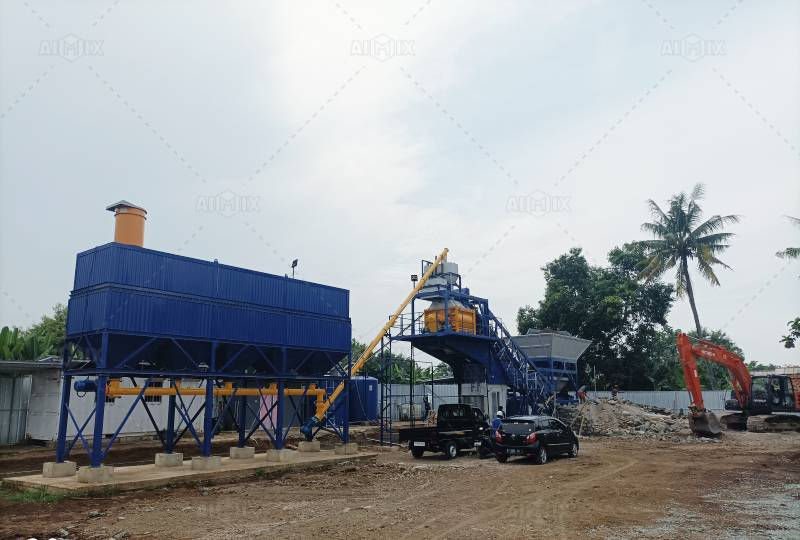
4. High-Capacity and High-Efficiency Mixers
To meet the increasing demand for high-volume concrete production, modern concrete mixer plants are equipped with high-capacity and high-efficiency mixers. These advanced mixers are designed to handle larger volumes of concrete with faster mixing times, without compromising on quality. New mixing technologies, such as planetary and twin-shaft mixers, are being adopted in concrete mixer plants to achieve better homogeneity and consistency in the final product.
These high-efficiency mixers not only improve productivity but also reduce energy consumption. The ability to mix larger quantities of concrete in a shorter amount of time increases the overall throughput of the plant, making it more profitable for plant operators. Additionally, these mixers are designed with durability in mind, ensuring long-lasting performance and minimizing maintenance costs.
5. Smart Integration and IoT in Concrete Mixer Plants
The Internet of Things (IoT) is transforming the construction industry, and concrete mixer plants are no exception. IoT-enabled sensors and devices are being integrated into plants to collect real-time data on various operational parameters, such as temperature, humidity, and equipment performance. This data is transmitted to a central cloud-based system, where it can be analyzed and used to make informed decisions.
For example, IoT sensors can monitor the moisture content of aggregates and adjust the water-to-cement ratio accordingly. This ensures that the concrete produced meets the required strength and durability specifications. Furthermore, predictive maintenance powered by IoT can help identify potential equipment failures before they occur, reducing downtime and repair costs.
Concrete batch plant manufacturers are increasingly adopting IoT-based solutions to offer customers better control over their operations and improve efficiency. The integration of smart technologies allows operators to make data-driven decisions, leading to optimized performance and higher quality standards.
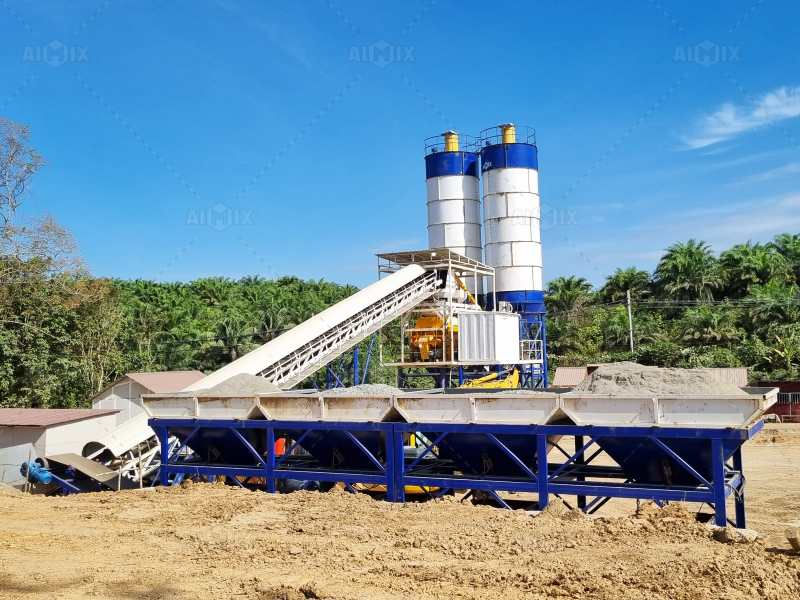
6. Improved Mixing Technology for Specialty Concrete
The growing demand for specialty concrete, such as high-strength, self-compacting, and decorative concrete, has prompted concrete mixer plants to adopt new mixing technologies. Advanced mixers are now designed to handle these unique concrete types, which require precise mixing techniques and careful control over the properties of the mix.
Self-compacting concrete (SCC), for instance, requires highly efficient mixing to achieve its flowability and workability without the need for vibration. To produce this type of concrete, mixer plants are equipped with specialized mixing blades and high-speed mixing capabilities. Similarly, the production of high-strength concrete demands precise control over the mix's water-to-cement ratio and the use of high-quality aggregates. Concrete mixer plants are evolving to accommodate these needs, ensuring that even the most demanding concrete mixes are produced efficiently.
Conclusion
Innovative technologies in concrete mixer plants are transforming the construction industry by enhancing performance, improving sustainability, and meeting the growing demand for high-quality concrete. From automation and control systems to energy-efficient motors and the integration of IoT, these technologies are driving improvements in both productivity and environmental responsibility. As the industry continues to evolve, ready mix concrete batch plants and concrete batch plant manufacturers will play a key role in shaping the future of concrete production, ensuring that it meets the needs of a rapidly changing world.
By embracing these innovations, concrete mixer plants are becoming more efficient, cost-effective, and environmentally friendly, paving the way for a more sustainable construction industry.
Comments