RMC Plants: A 360-Degree View of Their Impact on Construction
- aimixglobal5
- Jan 14
- 4 min read
Ready-mix concrete (RMC) plants have become a cornerstone of modern construction, offering significant advantages over traditional methods of concrete production. As construction projects scale in complexity and speed, the demand for high-quality, reliable, and efficiently produced concrete has surged. RMC plants provide a comprehensive solution to meet these needs, and understanding their impact on the construction industry from a 360-degree perspective reveals why they are indispensable to contemporary building practices.
What are RMC Plants?
Ready mix concrete plants are facilities designed to mix concrete ingredients—such as cement, aggregates, water, and additives—into a homogeneous mixture, which is then delivered to construction sites in the required quantities. The concrete is typically mixed in batches, ensuring that it meets the precise specifications needed for the project. Unlike traditional methods, where concrete is mixed on-site, RMC plants prepare concrete in a controlled environment, which significantly improves quality and consistency.
RMC plants are equipped with automated batching systems, ensuring that precise proportions of raw materials are mixed to produce concrete that meets the highest standards of strength, durability, and workability. Additionally, they are designed for large-scale production, making them ideal for handling the demands of major construction projects such as highways, commercial buildings, and large residential developments.
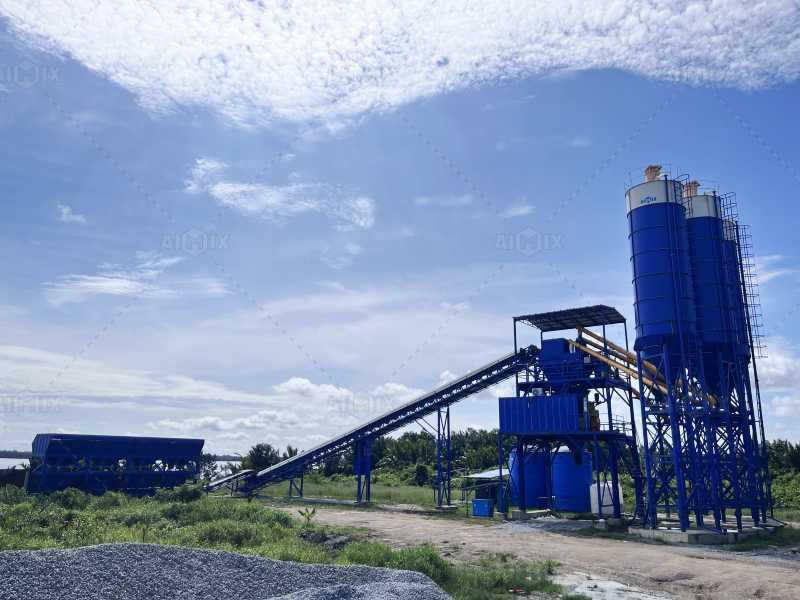
Enhanced Efficiency and Time Savings
One of the most immediate benefits of RMC plants is the significant boost in efficiency they offer to construction projects. Traditional concrete mixing on-site can be time-consuming and subject to variability in mix quality, which can delay projects and increase costs. RMC plants, on the other hand, produce concrete in large quantities at the plant and transport it to the construction site ready for use.
This efficiency saves valuable time during the construction process. With ready-mixed concrete, contractors can avoid delays caused by waiting for the concrete to be mixed on-site. Since the concrete is delivered in precise amounts, construction teams can also avoid excess or shortage of material, ensuring that the project progresses smoothly without unnecessary interruptions.
Moreover, RMC plants can cater to multiple projects simultaneously, providing a steady supply of concrete to various job sites. This ensures that large construction firms can handle multiple projects with ease, reducing project downtime and improving overall productivity.
Improved Quality Control
Consistency and quality are paramount in concrete production, particularly when used for large-scale, long-lasting structures. At traditional on-site mixing locations, variables such as weather, human error, and inconsistent materials can result in uneven batches and unpredictable outcomes. This can compromise the strength, durability, and workability of the concrete, which, in turn, can affect the integrity of the entire structure.
RMC plants use advanced automated systems that monitor and control the entire mixing process. The ingredients are measured with high precision, ensuring that every batch of concrete is consistent with the desired specifications. This level of quality control results in a more reliable final product that is less prone to defects or inconsistencies. With RMC plants, construction companies can be confident that the concrete they are using will meet all the necessary strength and durability requirements.
Additionally, the use of high-quality materials and additives ensures that the concrete produced at RMC plants is more durable and weather-resistant, which is particularly important for projects in harsh environments. RMC plants can also produce specialized concrete mixes, such as self-compacting concrete or high-strength concrete, that are tailored to specific project needs.

Cost Efficiency and Waste Reduction
Ready-mix concrete plants provide significant cost savings for construction companies. When mixing concrete on-site, there is a risk of over-ordering or under-ordering materials, which can lead to wasted resources or delays. RMC plants eliminate this problem by delivering the precise amount of concrete needed for the job. This reduces waste and ensures that contractors only pay for what they use.
Furthermore, by reducing material wastage and improving efficiency, RMC plants help lower the overall cost of the project. The improved accuracy of material delivery also reduces the need for excess labor and equipment on-site, which can result in additional cost savings.
RMC plants are also more environmentally friendly compared to traditional on-site mixing, as they minimize the environmental impact associated with excess concrete waste. Concrete that is not used in one project can be recycled or repurposed for other projects, reducing the need for new raw materials and helping to minimize the carbon footprint of the construction process.
Scalability for Large Projects
RMC plants play a pivotal role in large-scale construction projects that require substantial quantities of concrete. These concrete mixer plants are designed to produce concrete in large volumes, making them ideal for projects that demand consistent, high-quality material in vast quantities. Whether it’s a multi-story building, a bridge, or an expansive highway, RMC plants have the capacity to handle the volume requirements of major projects without compromising quality or delivery schedules.
In addition to their production capabilities, RMC plants are equipped to manage multiple deliveries at once, ensuring that large projects receive the materials they need on time. This scalability is essential for meeting deadlines and staying on track during the construction process, especially when dealing with tight timelines.
Sustainability and Environmental Benefits
The growing emphasis on sustainability in the construction industry has made RMC plants an attractive option for environmentally-conscious developers. RMC plants are designed to optimize the use of resources, reducing waste and energy consumption. Additionally, many plants are incorporating eco-friendly practices such as recycling water and reusing concrete.
Modern RMC plants also have the capability to produce low-carbon concrete, which can help reduce the environmental impact of construction projects. By adopting green practices, RMC plants can contribute to the construction industry’s efforts to meet sustainability goals and reduce carbon emissions.
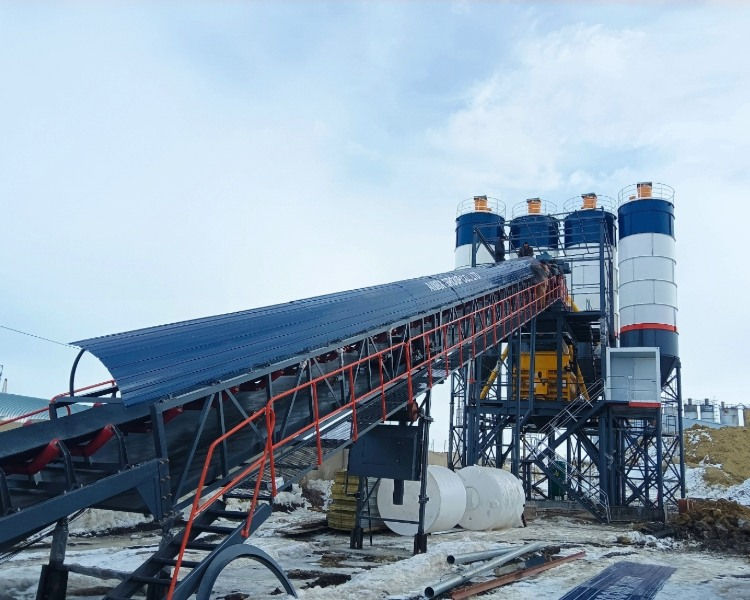
Conclusion: The Future of Construction with RMC Plants
From a 360-degree perspective, the impact of RMC plants on the construction industry is undeniable. They offer improved efficiency, better quality control, cost savings, scalability, and environmental benefits that are transforming how projects are managed. As the construction industry continues to evolve, the demand for ready-mixed concrete will only increase, making RMC plants a critical component of modern infrastructure development.
By investing in RMC plants, construction companies can ensure that they meet the growing demands of large-scale projects while improving the quality of their output and reducing their environmental footprint. With these advantages, ready-mix concrete plants are not just a practical solution—they are a game-changer for the future of construction.
Comments