System Design and Its Role in Concrete Mixing Plant Price Variation
- aimixglobal5
- Jul 10
- 4 min read
When evaluating a concrete mixing plant for purchase, one of the most important—but often overlooked—factors is system design. While many buyers initially focus on capacity, brand, or mobility, it's the internal configuration, automation level, and structural layout that often have the greatest impact on the concrete mixing plant price.
Understanding how system design influences pricing can help buyers make informed investment decisions and avoid overpaying for features they may not need—or worse, underinvesting in critical components that affect plant performance and long-term ROI.

What Is “System Design” in a Concrete Mixing Plant?
In the context of a concrete mixing plant, system design refers to the way the plant is structured, configured, and equipped to carry out all concrete production functions. This includes:
Weighing and batching systems (aggregate, cement, water, additives)
Mixing system (twin-shaft, planetary, or drum mixers)
Control system (manual, semi-automatic, or full PLC automation)
Storage and delivery systems (aggregate bins, silos, conveyors, discharge chutes)
Mobility type (stationary, mobile, or compact modular systems)
Each of these design choices has a direct influence on the overall price of a concrete mixing plant.
Type of Mixing System and Its Cost Implications
One of the most price-sensitive components is the mixing system itself. There are generally three types:
Twin-shaft mixers: High-efficiency mixing with short cycles; ideal for large-scale commercial use. These are more expensive but offer excellent uniformity and fast throughput.
Planetary mixers: Ideal for precast and specialty concrete where precision is key. Mid to high price range depending on capacity.
Drum mixers: Common in small or mobile concrete batching plants; more affordable but lower performance for demanding mixes.
The more robust and advanced the mixer, the higher the concrete mixing plant price—but also the higher the efficiency and quality control.
Degree of Automation in the Control System
System design also encompasses the level of automation used to control batching, weighing, and mixing:
Manual systems: Low-cost, but require skilled labor and prone to human error.
Semi-automatic: Moderate pricing, balances control with user input.
Fully automatic PLC systems: Higher upfront cost but offer real-time monitoring, recipe storage, and remote operation.
An automated control system can add several thousand dollars to the plant’s base cost, but it drastically reduces labor costs and improves batch accuracy over time.

Aggregate Storage and Feeding Layout
The layout of the aggregate feeding and storage system affects both land usage and plant complexity. Typical options include:
Inline aggregate bins: Compact and ideal for small areas, but limited in capacity.
Ground hopper + skip hoist: Lower initial cost, but slower feeding speed.
Belt conveyor systems: Faster and more efficient but adds to the overall plant cost due to extra components.
The number and size of aggregate bins also impact concrete mixing plant price. A plant with 4–5 bins will naturally cost more than one with 2 bins, but it allows for greater material flexibility and batch customization.
Mobility and Structural Design
The mobility type of the plant plays a major role in its pricing:
Stationary concrete mixing plants: Generally lower price per capacity unit but require foundation work and longer setup time.
Mobile concrete mixing plants: More expensive due to chassis, compact layout, and fast-setup systems.
Modular plants: Offer both flexibility and scalability, but may include premium pricing due to ease of disassembly and transportation.
For project-based operations or remote site work, the extra cost of mobile or modular design is justified by reduced installation time and enhanced transportability.
Customization and Additional Components
Every customization—whether it’s adding a screw conveyor, admixture dosing system, dust collector, or hot water system—adds to the plant's final price. For example:
Cement silos: Single vs. multiple silo systems significantly impact the price.
Moisture sensors: Improve batching precision but add technical cost.
Fiber dosing units: Required in specialized concrete production, increasing automation and equipment complexity.
A basic concrete mixing plant may start at $30,000 to $60,000, while a high-end customized plant with multiple silos, full PLC, and advanced batching tech can exceed $150,000 or more.
Energy Efficiency and Environmental Design
Energy-saving components such as variable frequency drives (VFDs), insulated panels, and eco-dust collection systems are becoming more common. While they increase initial concrete mixing plant price, they also:
Lower long-term operational costs
Help comply with local environmental regulations
Improve plant sustainability profile for eco-conscious clients
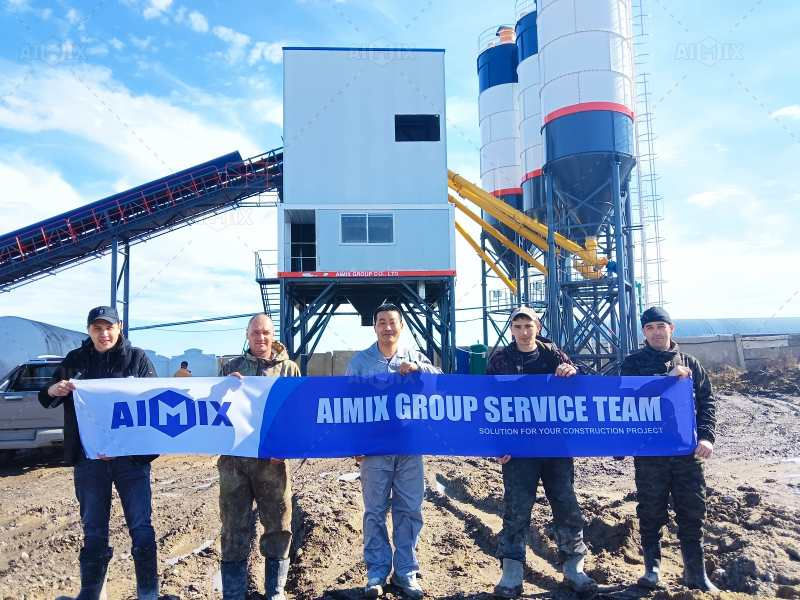
Final Thoughts: Choose the Right Design for the Right Price
System design is more than just an engineering detail—it’s a key determinant in the price, performance, and profitability of a concrete mixing plant. When evaluating plants for sale, buyers should not only compare prices but also scrutinize the internal structure and automation level.
To balance cost and capability:
Identify your production needs (volume, mix types, mobility).
Match the system design to your workflow.
Consider long-term savings from automation and efficiency features.
In short, the concrete mixing plant price isn’t just about what you pay upfront—it’s about what you gain in quality, speed, and operational peace of mind.
Comments