Transforming a Concrete Mixture Pump into Mortar Spraying Equipment
- aimixglobal5
- Feb 10
- 4 min read
In modern construction, versatility and efficiency are paramount. Equipment that can serve multiple purposes offers significant advantages in terms of cost savings, space management, and operational flexibility. One such piece of equipment that can be adapted for various uses is the concrete mixture pump. Originally designed to transport and place concrete, these pumps can be modified to function as mortar spraying equipment. By making specific adjustments and adaptations, a concrete mixture pump can be transformed to handle the different material properties and application techniques required for spraying mortar. This passage will explore the process of converting a concrete mixture pump into mortar spraying equipment, including the benefits of this transformation, the technical modifications needed, and practical considerations for successful operation.

Understanding the Equipment
A concrete mixture pump is a powerful tool primarily used to convey concrete from a mixing station to the application site. It consists of a hopper for receiving the concrete mix, a pumping mechanism to propel the mixture through a pipeline, and a delivery nozzle for precise placement. Mortar spraying equipment, on the other hand, is designed to apply a thin, even layer of mortar onto surfaces such as walls, ceilings, and floors. Mortar has a different consistency and particle size compared to concrete, which necessitates certain modifications to the pump to ensure efficient spraying and adherence.
Benefits of Converting a Concrete Mixture Pump
1. Cost Efficiency: By converting an existing concrete mixture pump into mortar spraying equipment, construction companies can save on the cost of purchasing separate machinery for each task. This dual functionality reduces the need for additional capital expenditure and maintenance costs.
2. Space Management: Utilizing one piece of equipment for multiple purposes helps in better space management on construction sites. It reduces the clutter of having multiple machines and makes the site more organized.
3. Operational Flexibility: Having equipment that can switch between pumping concrete and spraying mortar provides greater flexibility in planning and executing various construction tasks. It enables quick adaptation to different project requirements without the need for extensive setup changes.
4. Enhanced Productivity: The ability to switch functions quickly can lead to increased productivity, as crews can move from one task to another without waiting for additional equipment to arrive or be set up.
Technical Modifications for Conversion
1. Nozzle Adaptation: The nozzle used for spraying mortar needs to be different from the one used for placing concrete. Mortar spraying requires a finer, more controlled spray pattern to ensure even coverage. This can be achieved by replacing the concrete nozzle with a specialized mortar spraying nozzle that has a smaller orifice and better atomization capabilities.
2. Pipeline Adjustments: The pipeline used for transporting mortar should have a smaller diameter compared to that used for concrete. This helps in maintaining the necessary pressure and flow rate for spraying. In some cases, it might be necessary to replace the pipeline entirely or add adapters to reduce the diameter.
3. Pump Pressure Settings: Mortar has a different viscosity and consistency than concrete, requiring adjustments to the pump's pressure settings. Lowering the pump pressure can help achieve a smoother flow and prevent clogging. It is essential to refer to the concrete pump manufacturer guidelines for the appropriate pressure settings when handling mortar.
4. Mix Consistency: The consistency of the mortar mix needs to be adjusted to ensure proper spraying. Mortar should be more fluid than concrete to pass through the finer nozzle and pipeline. This can be achieved by increasing the water content or adding specific admixtures designed to enhance flowability without compromising the mortar's strength and adhesion properties.
5. Hopper Modifications: The hopper of the concrete mixture pump may need modifications to handle the finer particles and different consistency of mortar. Installing a mesh screen or filter can help prevent larger particles or debris from entering the pump mechanism, reducing the risk of blockages.
Practical Considerations for Operation
1. Material Compatibility: Ensure that the materials used in the pump, pipeline, and nozzle are compatible with the mortar mix. Some materials used for concrete may not withstand the abrasive nature of certain mortar mixes, leading to premature wear and tear.
2. Training and Safety: Proper training for operators is crucial to ensure safe and effective use of the converted equipment. Operators should be familiar with the adjustments and modifications made to the pump and understand the differences in handling and applying mortar compared to concrete.
3. Maintenance and Inspection: Regular maintenance and inspection of the equipment are essential to ensure its longevity and reliable performance. Check for any signs of wear, especially in the nozzle and pipeline, and replace components as needed to prevent operational issues.
4. Testing and Calibration: Before using the converted pump on a project, conduct thorough testing and calibration to ensure that the mortar is being sprayed evenly and consistently. This step helps identify any potential issues and allows for fine-tuning of the equipment settings.
5. Project Planning: Consider the specific requirements of each project when planning to use the converted pump. Factors such as the type of surface, the required thickness of the mortar layer, and environmental conditions can influence the choice of settings and materials.
Converting a concrete mixture pump into mortar spraying equipment is a practical and cost-effective solution for construction projects requiring versatile machinery. By making specific technical modifications and considering practical operational factors, a concrete mixture pump can be effectively transformed to handle the different properties and application techniques of mortar. This dual functionality not only enhances operational flexibility but also contributes to significant cost savings and improved productivity on construction sites. With proper training, maintenance, and testing, the converted equipment can deliver reliable and efficient performance, meeting the diverse needs of modern construction projects.
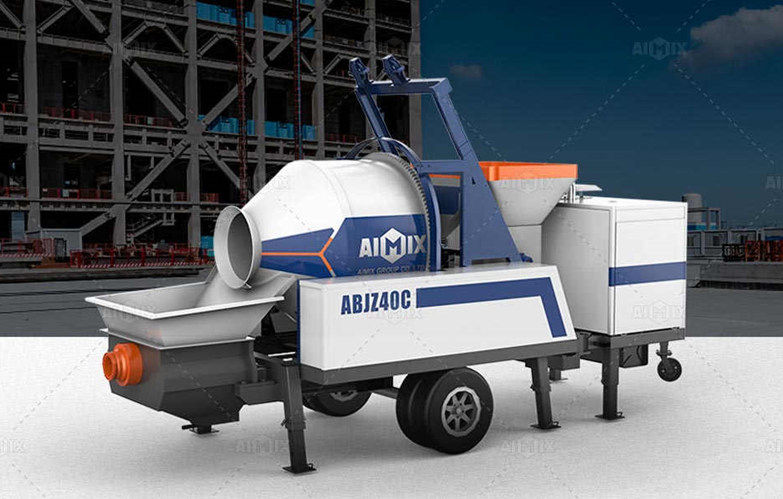
Comments