Understanding RMC Plant Cost from a Mechanical Engineering Perspective
- aimixglobal5
- May 12
- 3 min read
Investing in a Ready-Mix Concrete (RMC) plant requires a deep understanding of not just upfront pricing but also the technical intricacies that influence cost and long-term performance. From a mechanical engineering perspective, the cost of an RMC plant is shaped by key components such as batching systems, mixers, conveyors, structural design, and energy efficiency. This article explores the breakdown of RMC plant cost with a focus on engineering factors—and how they ultimately impact the ready mix concrete plant profit margin.

1. Core Mechanical Components and Their Impact on Cost
A ready-mix concrete plant typically includes the following major systems:
Aggregate Batching Machine
Cement Silo
Weighing System
Mixing Unit (e.g., twin shaft or planetary mixer)
Control Panel and Automation System
Conveyor Belts or Skip Hoist
Water and Additive Supply System
From an engineering standpoint, each of these components contributes to both the initial investment and operational efficiency. For instance:
Twin shaft mixers cost more than planetary or drum mixers but offer better mixing performance for large-volume operations.
Fully automated control systems increase plant price but improve precision and productivity, reducing waste and improving consistency.
The design and quality of steel structures, the thickness of wear-resistant linings in the mixer, and the quality of load cells also affect long-term reliability and, consequently, the profit margin.
2. Equipment Capacity and Configuration
One of the most significant technical factors affecting RMC plant cost is capacity, typically measured in cubic meters per hour (e.g., 25 m³/h, 60 m³/h, 120 m³/h).
Small-scale RMC plants (25–50 m³/h) are less costly and suitable for local residential or rural projects.
Medium-to-large-scale plants (60–120+ m³/h) are more capital-intensive but deliver greater economies of scale.
Configuration type also matters:
Stationary RMC plants are designed for long-term use at fixed sites and cost more due to permanent foundation work and larger silos.
Mobile plants, with trailer-mounted components, offer portability but usually come with lower output and smaller silos, reducing cost but also limiting throughput.
Engineers must assess the project scale, concrete demand, and site mobility before choosing the right capacity and configuration.
3. Mechanical Design and Energy Efficiency
Modern RMC plants are increasingly evaluated not only by cost but also by energy efficiency and mechanical reliability. Factors such as:
Motor power rating and energy usage per cubic meter of concrete
Belt vs. skip hoist systems (skip hoist saves space but limits capacity)
Reinforcement and wear protection in mixers
Dust collection and water recycling systems
All of these affect both initial pricing and ongoing operating costs. A more efficient plant might cost more upfront but will improve ready mix concrete plant profit margins by lowering electricity bills, reducing maintenance frequency, and increasing uptime.

4. Installation, Maintenance, and Hidden Costs
From an engineering perspective, many buyers underestimate the total cost of ownership (TCO). Beyond machinery purchase, other cost factors include:
Foundation and civil works
Electrical connections and cabling
Calibration and test runs
Routine maintenance: bearing replacements, mixer blade wear, filter cleaning
Spare parts stock for mission-critical systems
Mechanical engineers often conduct lifecycle costing analysis to help determine how long it will take to recoup the investment through improved plant uptime and reduced downtime. Preventive maintenance planning is also key to sustaining profits.
5. Profit Margins: Engineering's Role in Financial Success
While civil engineers focus on mix design and concrete quality, mechanical engineers directly influence the ready mix concrete plant profit margin by:
Selecting efficient motors and reducers
Ensuring proper alignment of belts and shafts to reduce mechanical wear
Choosing modular parts for fast repairs
Designing ventilation and cooling to extend equipment life
Automating data monitoring to optimize batching precision
A well-designed plant can achieve 5%–15% higher operational efficiency, which translates into thousands of dollars in additional monthly profit—especially on large-volume projects.
6. Regional Variations in Cost
The mechanical cost of an RMC plant also varies by country due to:
Raw material prices (e.g., steel, motors, electronics)
Local labor rates for installation and maintenance
Import duties or tax regulations
Availability of local spare parts and service
For instance, an RMC plant in Pakistan or India might have lower upfront costs due to cheaper labor and materials, but buyers must ensure that mechanical components meet international standards to maintain long-term profitability.
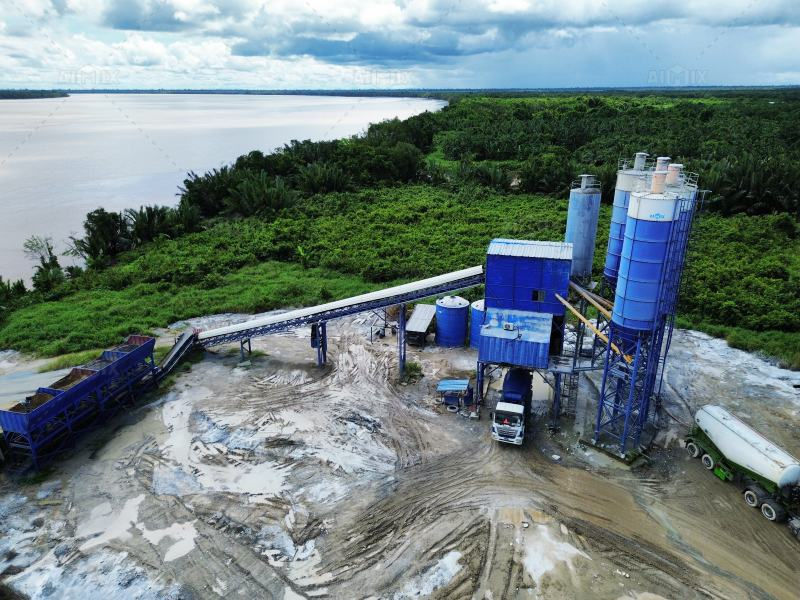
Conclusion: Engineering for Profit
Understanding RMC plant cost from a mechanical engineering perspective is crucial for making informed decisions. It's not just about price tags—it's about how efficiently a plant converts raw materials into high-quality concrete while minimizing energy use, maintenance downtime, and waste.
In the long run, the mechanical design of your RMC plant is directly tied to your profit margin. Investing in high-efficiency components, smart automation, and durable materials may increase initial cost—but pays off exponentially through smoother operations and higher output quality.
Comments