What is the Working Principle of Asphalt Plant and Its Components?
- aimixglobal5
- Feb 5
- 4 min read
Asphalt plants play a critical role in modern infrastructure projects, especially for road construction. Understanding how these plants work can help you make informed decisions when choosing the right equipment for your construction needs. In this article, we will delve into how an asphalt plant works, their components, and why they are essential for efficient and high-quality asphalt production.
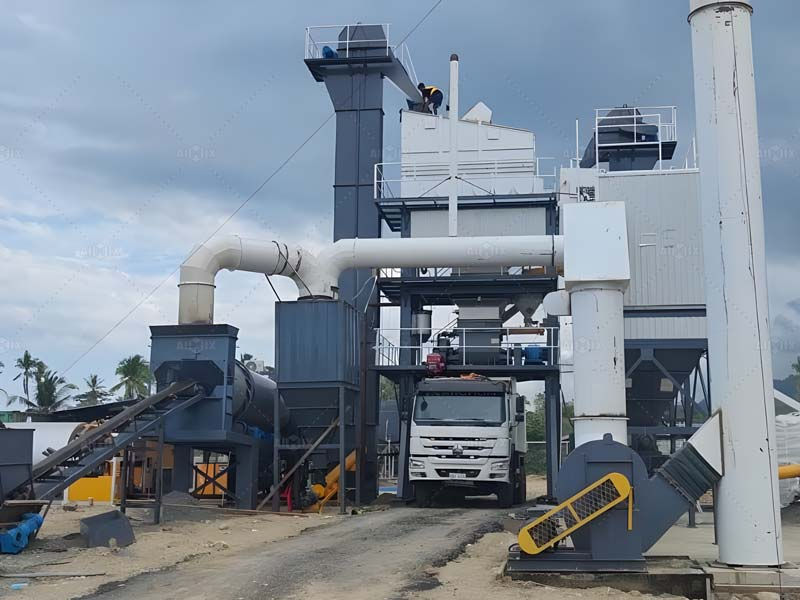
Understanding the Working Principle of an Asphalt Plant
An asphalt plant is designed to produce asphalt through a process called "mixing." This involves combining a precise amount of aggregate, binder, and additives in a controlled environment to create a durable and high-quality asphalt mix. The working principle can vary depending on the type of asphalt plant—batch or continuous. However, both types aim to ensure the right temperature, consistency, and quality of the final product.
Batch Asphalt Plants: Precision and Control
In a batch asphalt plant, the mixing process happens in discrete batches. The aggregates are heated and dried before being combined with the bitumen (asphalt binder). The process includes the following key steps:
Heating and Drying: Aggregates are heated to the right temperature, ensuring they are dry before mixing.
Mixing: Once the aggregates are ready, they are combined with bitumen in a mixer, forming the final asphalt mix.
Storage: The finished asphalt mix is stored in a silo, ready for transport to the construction site.
The batch process allows for precise control over the quality and consistency of each batch, making it ideal for projects requiring specific asphalt mix designs.
Continuous Asphalt Plants: Efficiency and Continuous Output
In contrast, continuous asphalt plants work by continuously feeding aggregates, bitumen, and additives into the plant, allowing for an uninterrupted production process. The components are mixed as they move through the system, producing a steady stream of asphalt. This type of plant is more efficient and suited for projects with a consistent demand for asphalt.
The continuous mixing process has several advantages:
High Output: Continuous production allows for larger quantities of asphalt to be produced over extended periods.
Cost-Effective: These plants can operate for long periods without downtime, making them more cost-effective for large projects.
Consistency: The continuous process ensures uniformity in the final asphalt mix.
The Key Asphalt Plant Components
Every asphalt plant consists of several critical components that ensure efficient asphalt production. Let’s take a closer look at these parts:
1. Cold Aggregate Feeder
The cold aggregate feeder is responsible for supplying the raw materials (aggregates) into the plant. These materials include crushed stones, sand, and gravel, which are stored in separate bins to ensure proper proportions before mixing.
2. Dryer Drum
The dryer drum is a rotating drum that heats and dries the aggregates. This component ensures that the aggregates reach the optimal temperature for mixing with bitumen. The drying process is crucial for preventing excess moisture in the final mix, which could affect the asphalt's performance.
3. Hot Aggregate Elevator
The hot aggregate elevator moves the dried aggregates to the next stage, where they will be combined with bitumen. It ensures smooth and efficient material handling during the production process.
4. Mixing Unit
The mixing unit is where the asphalt mix is created. Aggregates and bitumen are combined in this unit, along with any additives. The quality of the mix depends heavily on the efficiency of the mixing unit. Proper mixing ensures that the asphalt is homogeneous and ready for use.
5. Bitumen Storage and Pumping System
Bitumen, the key binder in asphalt, is stored in large tanks at high temperatures to maintain its viscosity. The pumping system ensures the bitumen is fed accurately into the mixing unit to achieve the correct binder ratio.
6. Control System
The control system of an asphalt plant manages and monitors the entire production process. Modern plants are equipped with sophisticated technology, allowing for automated operations, real-time monitoring, and adjustments to ensure the highest quality asphalt production.
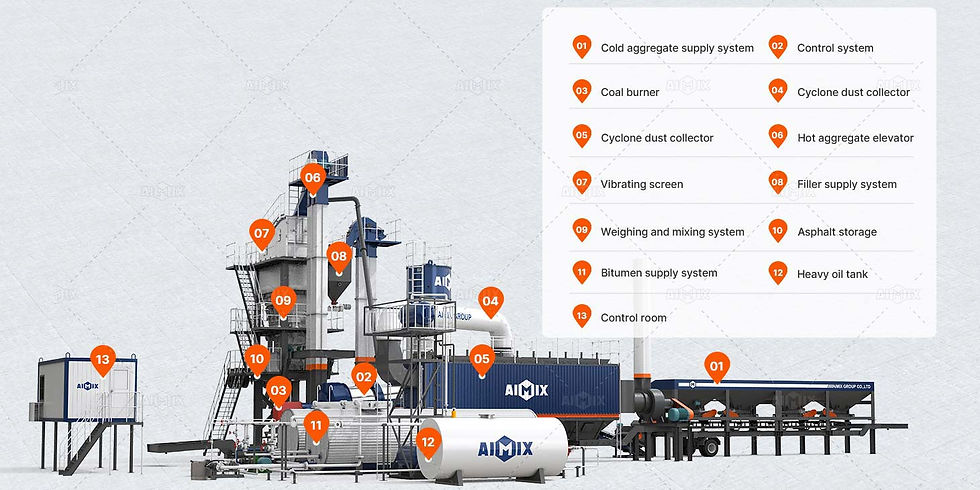
Why Choosing the Right Asphalt Plant Matters for Your Project
When selecting an asphalt plant for your construction project, it's essential to consider factors such as output requirements, budget, and project scale. Batch plants are ideal for small to medium-sized projects where precision is critical, while continuous plants are better suited for large-scale projects where efficiency and high output are prioritized.
At AIMIX, we offer both types of asphalt plants, tailored to meet the specific needs of different construction projects. Whether you're working on urban road repairs or large infrastructure projects in Indonesia, AIMIX's stationary asphalt mixing plant is built to deliver consistent quality and efficiency, ensuring the success of your project.
Conclusion
Understanding the working principle and components of an asphalt plant is vital for making the right choice for your construction needs. Whether you opt for a batch or continuous plant, the key is selecting a reliable and efficient plant that aligns with your project goals. AIMIX offers a range of asphalt plants designed for different requirements, ensuring high-quality asphalt production every time.
If you're looking for a durable and efficient asphalt plant, AIMIX is here to help. Contact us today to learn more about our asphalt plant solutions and how we can support your construction projects in Indonesia and beyond.
Comments