Energy Consumption Analysis of Transportation Process of Mobile Concrete Pump Boom for Sale
- aimixglobal5
- Jul 1
- 4 min read
In modern construction projects, efficiency and sustainability are at the forefront of every decision—including how equipment is transported to job sites. Among various machines used in concrete delivery, the mobile concrete pump is a critical player due to its ability to combine mobility with precision in concrete placement. When fitted with a boom arm, these machines—advertised as concrete pump boom for sale—offer extended reach and flexibility. However, before these machines even begin operation, they incur energy costs during transportation. Understanding the energy consumption involved in transporting mobile concrete pumps with booms is vital for contractors, equipment dealers, and environmental planners aiming to reduce both costs and environmental footprints.

Understanding the Structure and Weight Factors
The first consideration in analyzing energy consumption during transport is the structural makeup of the mobile concrete pump itself. A typical concrete pump truck with boom can weigh anywhere from 20 to 60 tons depending on the boom length, materials used, and whether the machine includes additional attachments. The boom structure—made of steel or alloy segments that fold or telescope—adds substantial weight. This mass affects fuel efficiency when transported on highways or urban roads.
When listed as a concrete pump boom for sale, such equipment often includes information about gross vehicle weight and axle load distribution. These figures directly impact the type of trailer or flatbed required for transport. Heavier units often need special permits, route planning, and escort vehicles, all of which contribute to increased energy consumption and fuel use during delivery.
Transportation Modes and Their Energy Impact
The method of transport significantly influences total energy usage. Most mobile concrete pump units are delivered by road using heavy-duty trailers or lowboys. The energy consumption here depends on three key factors: vehicle fuel efficiency, terrain conditions, and distance traveled.
For short-distance transport within a city or local region, fuel consumption per kilometer is moderate but constant idling during traffic congestion increases overall fuel use. On the other hand, long-distance highway transport may be more efficient per kilometer but adds cumulative fuel costs due to extended operation hours. A typical heavy truck carrying a concrete pump may consume 30 to 40 liters of diesel per 100 kilometers, translating into considerable energy usage for cross-region transportation.
When exporting a concrete pump boom for sale internationally, energy costs increase exponentially. The transport involves a combination of road movement to ports, shipping via container or roll-on/roll-off vessels, and sometimes additional road haulage in the destination country. Maritime shipping, although more fuel-efficient per ton-kilometer, still consumes massive amounts of bunker fuel, contributing to carbon emissions. In some cases, air freight is used for urgent delivery of smaller concrete pumps—but this is extremely energy-intensive and only viable for compact models without boom arms.
Fuel Type and Emissions
Diesel remains the dominant fuel for transporting mobile concrete pump units due to its availability and power output. Unfortunately, diesel trucks generate significant carbon dioxide (CO₂), nitrogen oxides (NOx), and particulate matter. The larger and heavier the machine, the more energy is required to move it, and thus, the more emissions are produced. Transporting a full-size concrete pump boom for sale across a country could result in the release of hundreds of kilograms of CO₂, especially if the route includes steep gradients or stop-and-go traffic in urban zones.
Some logistics companies are now shifting to biodiesel or LNG-powered heavy trucks to reduce emissions. While the impact on total energy consumption may be minimal, the carbon footprint can be reduced by as much as 30%, aligning with the sustainability goals of eco-conscious construction firms.
Route Planning and Load Efficiency
An often-overlooked factor in energy analysis is how well transportation is planned. Transporting a mobile concrete pump on an optimized route with minimal elevation gain, fewer urban bottlenecks, and steady-speed highways can reduce fuel consumption by up to 15%. Poor planning that results in backtracking, extended detours, or multiple stops can unnecessarily inflate energy use.
Additionally, shipping equipment in a disassembled state (where permitted) can also reduce energy costs. Some suppliers offering concrete pump boom for sale allow partial disassembly for easier container loading, reducing volume and possibly weight, depending on configuration. This method helps cut down the number of trips or containers needed and improves vehicle fuel efficiency due to lower drag and better axle weight distribution.
Packaging and Loading Efficiency
The way the mobile concrete pump is prepared for shipping can influence energy efficiency. Well-secured, balanced loads reduce drag, improve road safety, and enable consistent driving speeds, all of which contribute to fuel savings. When pumps are poorly loaded or unstable, drivers are forced to brake more often and drive at slower speeds, increasing fuel use and reducing the efficiency of the journey.
Additionally, optimized packaging for export reduces wasted cargo space. This is especially relevant when transporting multiple units in a batch. By reducing the number of shipments through effective space usage, companies reduce the overall energy footprint of their logistics operations.
Final Delivery and Onsite Positioning
The energy consumed doesn’t end at transport to the site. Final positioning of the mobile concrete pump—especially if the site is remote, muddy, or uneven—may require additional equipment like cranes or support vehicles, further adding to total energy use. Off-road fuel consumption is often much higher due to rough terrain and reduced tire efficiency.
In certain urban or restricted-access projects, smaller support trucks must ferry components individually, increasing trips and fuel use. Thus, final delivery logistics should be integrated into overall energy consumption calculations for the complete transportation process.
The energy consumption associated with transporting a mobile concrete pump, especially one equipped with a boom, is significant and influenced by numerous variables—from machine weight and fuel type to transport methods and loading efficiency. When listed as a concrete pump boom for sale, both buyers and sellers should consider not just purchase price but the hidden environmental and fuel costs of getting the machine onsite. Through better route planning, smarter fuel choices, and optimized packaging, construction companies and logistics providers can significantly reduce the energy footprint of transporting these vital machines—making each concrete pour just a bit more sustainable.
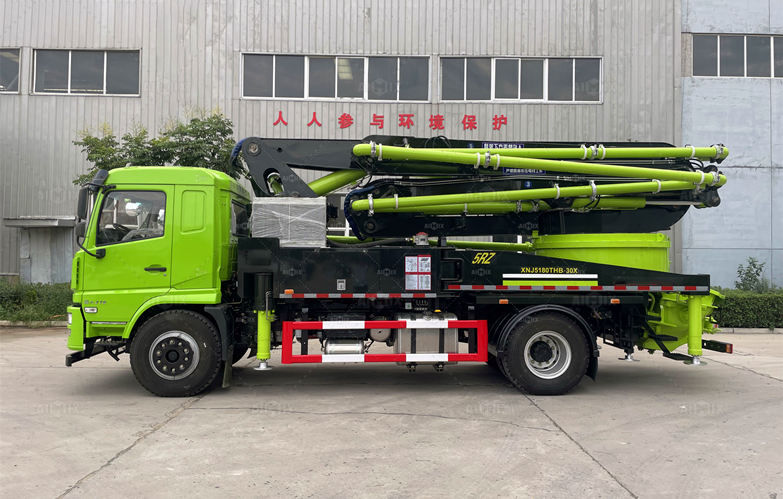
Comments