Evaluating the Operational Efficiency of Concrete Plants for Sale
- aimixglobal5
- Aug 19, 2024
- 4 min read
When purchasing a concrete plant, evaluating its operational efficiency is crucial to ensuring that it meets the demands of your construction projects and provides value for your investment. Operational efficiency directly impacts productivity, cost-effectiveness, and the overall quality of the concrete produced. This article provides a comprehensive guide on how to assess the operational efficiency of concrete plants for sale, focusing on key factors such as performance metrics, technology, maintenance, and overall plant design.
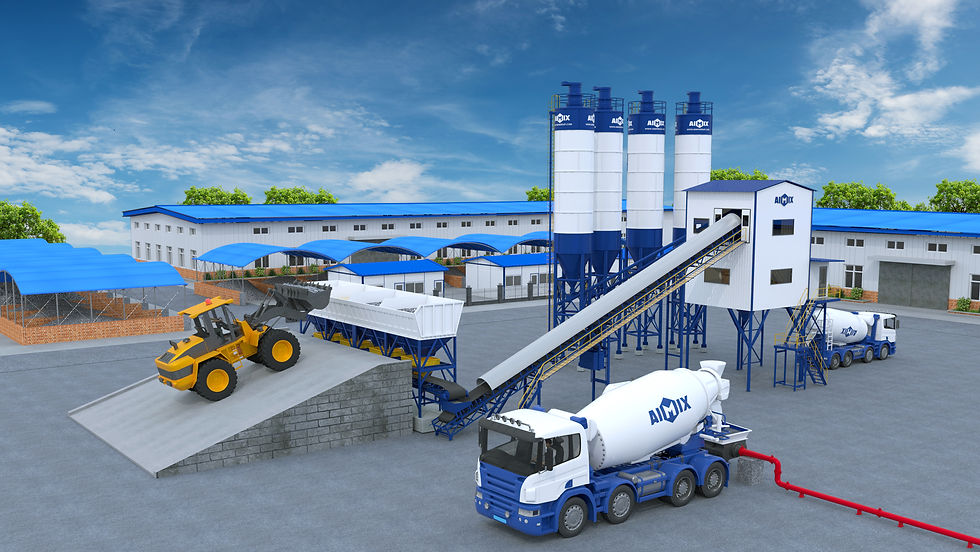
Performance Metrics
Understanding the performance metrics of a concrete plant is essential for evaluating its efficiency. Key metrics include production capacity, batching accuracy, and mixing time.
Production Capacity: Assess the plant’s production capacity, which indicates how much concrete it can produce within a given timeframe. This metric should align with your project needs and anticipated demand. Concrete plants come in various sizes and capacities, from small portable plants to large fixed installations. Consider whether the plant’s capacity will meet your current and future production requirements.
Batching Accuracy: The accuracy of the batching process affects the quality of the concrete produced. A plant with high batching accuracy ensures that the proportions of cement, aggregates, and water are precisely controlled, leading to consistent mix quality. Check if the plant has automated batching systems and how frequently they are calibrated to maintain accuracy.
Mixing Time: Efficient mixing time is critical for achieving a homogenous concrete mix. Evaluate the mixing equipment used in the plant, such as twin-shaft or planetary mixers, and their performance in terms of mixing speed and quality. Shorter mixing times with consistent results can enhance productivity and reduce the time needed for concrete preparation.
Technology and Automation
The integration of technology and automation in a concrete plant can significantly impact its operational efficiency. Modern plants are equipped with advanced systems that streamline processes and improve overall performance.
Control Systems: Evaluate the plant’s control systems, including the use of programmable logic controllers (PLCs) and human-machine interfaces (HMIs). These systems facilitate precise control over the batching and mixing processes, reducing human error and increasing efficiency. Check for features such as real-time monitoring, automated adjustments, and remote access capabilities.
Data Analytics: Advanced concrete plants often incorporate data analytics to monitor performance and optimize operations. Analyze how the plant collects and utilizes data on production metrics, equipment performance, and quality control. Data analytics can help identify inefficiencies, predict maintenance needs, and improve overall plant performance.
Remote Monitoring: Remote monitoring systems allow operators to oversee plant operations from off-site locations. Assess the plant’s remote monitoring capabilities, including real-time data access, performance tracking, and troubleshooting. Remote access can enhance operational flexibility and responsiveness, particularly in large or complex projects.

Maintenance and Reliability
The maintenance requirements and reliability of a concrete plant play a crucial role in its operational efficiency. Regular maintenance ensures that the plant remains in good working condition and minimizes the risk of unexpected breakdowns.
Maintenance Schedule: Review the plant’s maintenance schedule and procedures. Regular preventive maintenance helps identify and address potential issues before they lead to significant problems. Check if the plant’s manufacturer provides a detailed maintenance plan and support services to ensure ongoing reliability.
Equipment Reliability: Assess the reliability of the plant’s equipment, including mixers, conveyors, and batchers. Reliable equipment reduces the likelihood of downtime and ensures consistent production. Consider the track record of the equipment brand and whether spare parts are readily available.
Training and Support: Evaluate the level of training and support provided by the plant’s manufacturer or supplier. Proper training for plant operators and maintenance personnel can improve efficiency and reduce the likelihood of operational issues. Ensure that support services are available for troubleshooting and repairs.
If you are looking for reliable concrete batching plant, you are suggested to choose one from here https://aimixgroup.com/concrete-batching-plant/
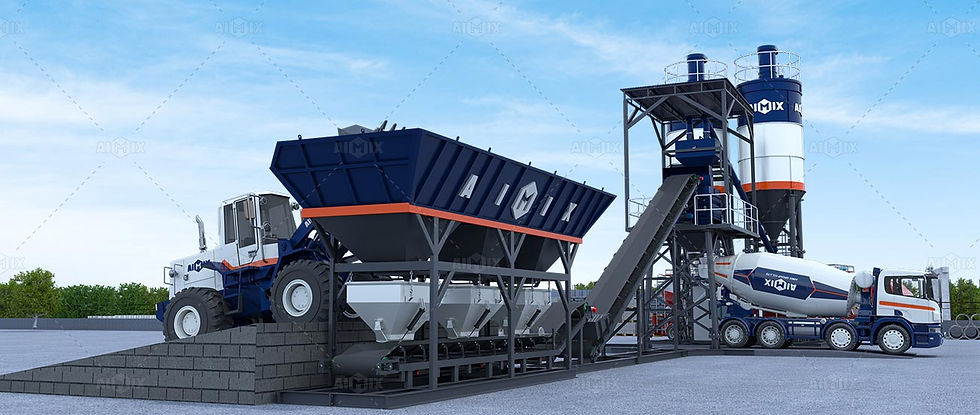
Plant Design and Layout
The design and layout of the concrete plant can influence its operational efficiency by affecting workflow, material handling, and overall functionality.
Layout Optimization: Assess the plant’s layout to ensure that it facilitates smooth material flow and minimizes handling time. An optimized layout positions storage areas, mixing equipment, and dispatch points to reduce transportation distances and streamline operations. Consider how the layout supports efficient material handling and access for maintenance.
Space Utilization: Efficient use of space is essential, especially in plants with limited room. Evaluate how the plant’s design maximizes space while accommodating all necessary equipment and processes. A well-designed layout can enhance productivity and reduce operational bottlenecks.
Safety and Accessibility: Ensure that the plant’s design incorporates safety features and provides easy access to all areas. Proper lighting, ventilation, and safety measures contribute to a safer working environment and improve overall operational efficiency. Check for clear pathways, safe storage for hazardous materials, and accessible maintenance areas.
Energy Efficiency and Sustainability
Energy efficiency and sustainability are increasingly important considerations in evaluating the operational efficiency of concrete plants. Implementing energy-efficient practices can reduce operating costs and minimize environmental impact.
Energy-Efficient Equipment: Look for energy-efficient equipment and technologies, such as variable frequency drives (VFDs) and energy-efficient motors. Energy-efficient equipment reduces energy consumption and operating costs while maintaining high performance.
Sustainable Practices: Evaluate the plant’s commitment to sustainable practices, such as water recycling and waste management. Implementing systems for recycling water used in concrete production and managing waste materials can contribute to environmental responsibility and cost savings.
Green Certifications: Consider whether the plant is designed to meet green building standards or certifications. Incorporating eco-friendly design elements and pursuing certifications can enhance the plant’s reputation and appeal to environmentally conscious clients.
Evaluating the operational efficiency of concrete plants for sale involves a thorough assessment of performance metrics, technology, maintenance requirements, plant design, and sustainability practices. By considering these factors, you can ensure that the plant you choose meets your production needs, operates efficiently, and delivers high-quality concrete. Investing time in a detailed evaluation process will help you make an informed decision and select a concrete plant that provides long-term value and supports the success of your construction projects.
Comments