How Maintenance and Upkeep Affect the Cost of a Batching Plant
- aimixglobal5
- Sep 12, 2024
- 5 min read
Concrete batching plants are essential equipment for producing consistent, high-quality concrete in construction projects of all sizes. While the initial cost of acquiring and installing a batching plant is significant, it is essential to understand that long-term costs, such as maintenance and upkeep, can significantly impact the total cost of ownership. Regular maintenance is crucial for ensuring the plant operates efficiently and avoids costly breakdowns that could disrupt production and increase expenses.
In this article, we will explore how maintenance and upkeep affect the cost of batching plant, the importance of preventive maintenance, and practical strategies to minimize long-term costs.
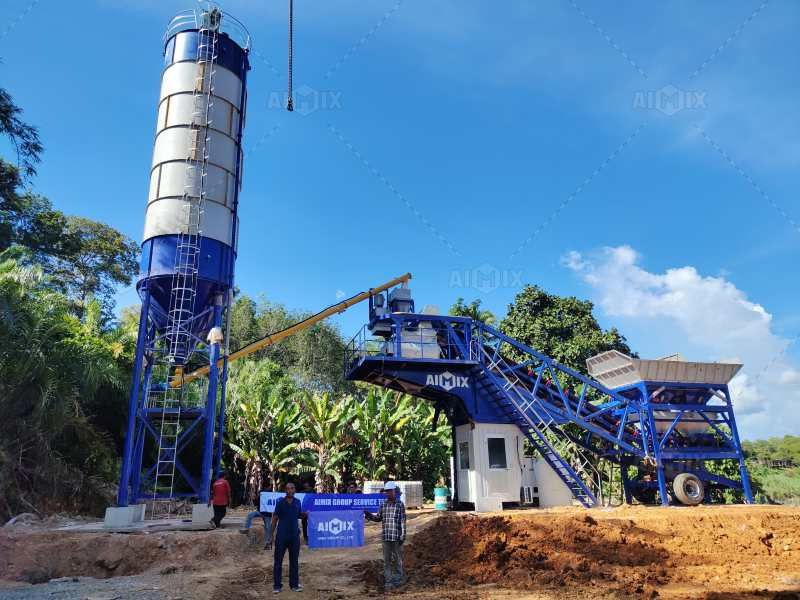
The Importance of Regular Maintenance
Concrete batching plants are complex systems made up of several critical components, including mixers, conveyors, silos, hoppers, and control systems. Each of these parts requires regular maintenance to function properly. Without proper upkeep, even minor issues can escalate into significant problems, leading to equipment failure, production delays, and costly repairs.
Preventive Maintenance: Preventive maintenance refers to routine inspections and servicing to detect and address potential issues before they become major problems. This includes tasks such as lubricating moving parts, checking belts and pulleys, inspecting electrical systems, and ensuring all components are clean and free from debris.
Avoiding Downtime: Downtime is one of the most significant cost factors associated with poorly maintained batching plants. If the plant experiences unexpected breakdowns, production comes to a halt, causing delays in project timelines. Depending on the scale of the project, downtime can lead to substantial financial losses, especially if deadlines are tight or penalties for delays are in place.
Direct Costs of Maintenance and Repairs
The cost of maintaining a batching plant consists of several components, including labor, parts, and any service contracts or third-party maintenance providers. Understanding these direct costs helps to assess the long-term expenses associated with keeping the plant operational.
Labor Costs: Maintenance requires skilled technicians who understand the intricate workings of batching plants. Whether you hire in-house personnel or outsource maintenance to a third-party service provider, labor costs are a recurring expense. Scheduling regular maintenance to reduce emergency repairs can help control labor costs over time.
Replacement Parts: As components wear out, they need to be replaced to ensure the plant continues to function smoothly. Common parts that require replacement include mixer blades, conveyor belts, filters, and valves. While these parts are not overly expensive, the cost can add up over time, especially if multiple components need replacement simultaneously. Using high-quality replacement parts may involve higher upfront costs, but they often last longer and reduce the frequency of repairs.
Repairs: Even with preventive maintenance, unforeseen issues can arise, leading to necessary repairs. The cost of repairs can vary depending on the severity of the problem, and some repairs may require specialized technicians, further increasing costs. Major repairs, such as replacing an entire motor or control system, can be expensive, both in terms of parts and labor.

The Hidden Costs of Poor Maintenance
Neglecting maintenance can result in more than just repair bills and downtime. Poor maintenance practices can lead to hidden costs that gradually erode profitability.
Energy Efficiency: When a batching plant is not properly maintained, it often operates less efficiently. For example, worn-out belts and pulleys can cause motors to work harder, increasing energy consumption. Over time, this leads to higher electricity costs. Routine maintenance ensures that the plant operates at optimal efficiency, keeping energy consumption—and costs—under control.
Reduced Lifespan of Equipment: One of the most significant hidden costs of poor maintenance is the reduced lifespan of the equipment. Without regular upkeep, components wear out faster, and the plant may need to be replaced or undergo major overhauls much earlier than anticipated. This results in higher long-term costs, as frequent equipment replacements are significantly more expensive than maintaining the original equipment.
Safety Risks: Poor maintenance can also increase the risk of accidents or injuries on the job site. Equipment that is not properly maintained may malfunction, potentially causing harm to workers and leading to costly liability claims. Additionally, safety violations due to inadequate maintenance can result in fines or penalties from regulatory authorities. In addition to these costs, do you want to know the batching plant prices? If so, you can check this https://aimixgroup.com/concrete-batching-plant/price-list/.

Preventive Maintenance Strategies to Reduce Long-Term Costs
To minimize long-term costs and ensure that your batching plant operates efficiently, it is essential to implement a comprehensive preventive maintenance plan. Here are a few strategies to consider:
Scheduled Inspections: Conduct regular inspections of all components, including mixers, conveyors, and electrical systems. This allows you to identify potential issues early and address them before they escalate. Inspections should be scheduled based on the manufacturer's recommendations and adjusted according to the plant’s usage frequency and environmental conditions.
Lubrication and Cleaning: Lubricating moving parts reduces friction and wear, extending the life of critical components. Additionally, keeping the plant clean by removing dust, debris, and hardened concrete from the machinery prevents blockages and damage to sensitive parts.
Staff Training: Ensuring that operators and maintenance personnel are properly trained can significantly reduce the risk of errors that lead to equipment damage. Trained staff can also identify early signs of wear or malfunction, allowing for quicker intervention.
Tracking Maintenance History: Maintain detailed records of all maintenance activities, including inspections, repairs, and replacements. This information helps you identify patterns in equipment wear and adjust maintenance schedules accordingly. Tracking maintenance history can also help you assess the total cost of upkeep and plan future budgets more accurately.
The Role of Warranties and Service Contracts
Many batching plant manufacturers offer warranties or service contracts that can help manage maintenance and repair costs. Warranties typically cover the cost of replacing faulty parts for a specified period, while service contracts provide regular maintenance services at a fixed cost.
Extended Warranties: Some manufacturers offer extended warranties for critical components like mixers or control systems. While purchasing an extended warranty involves an additional cost, it can provide peace of mind and help reduce unexpected repair expenses during the early years of the plant’s operation.
Service Contracts: Service contracts offer a structured maintenance plan, with regular inspections and repairs included. These contracts can simplify budgeting for maintenance, as the costs are spread out over time, making it easier to manage operational expenses.
Conclusion
Maintenance and upkeep play a critical role in the total cost of owning and operating a batching plant. By investing in regular preventive maintenance, you can reduce the risk of costly breakdowns, extend the lifespan of equipment, and ensure that your plant operates efficiently. While maintenance involves ongoing costs, neglecting it can lead to hidden expenses, reduced productivity, and safety risks. Ultimately, a well-maintained batching plant provides long-term savings, making it a smart investment for any construction business.
Comments