How to Use Station Pump Concrete
- aimixglobal5
- Oct 22, 2024
- 5 min read
Concrete pumping technology has revolutionized the construction industry by providing an efficient and effective method for delivering concrete to hard-to-reach places. Among the various types of concrete pumps, the stationary pump, also known as a station pump, stands out for its ability to handle large volumes of concrete over long distances. This technology is particularly useful in large-scale construction projects such as high-rise buildings, bridges, tunnels, and dams. This passage will provide a comprehensive guide on how to use a station pump concrete system, from setup to operation and maintenance.
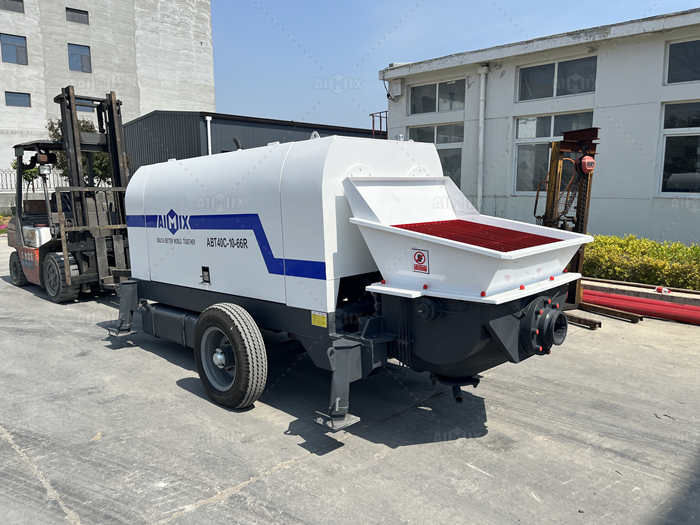
1. Understanding the Station Pump Concrete System
1.1 Components of a Station Pump
A station pump concrete system comprises several key components:
Pump Unit: The heart of the system, equipped with powerful hydraulic pumps that drive the concrete through the delivery pipeline.
Hopper: A large funnel-like container where concrete is poured before being pumped.
Delivery Pipeline: A series of pipes and hoses that transport the concrete from the hopper to the desired location.
Control Panel: An interface that allows operators to control the pump's functions, including the flow rate and pressure.
Accessories: Additional equipment such as pipe clamps, reducers, and cleaning tools.
1.2 Types of Station Pumps
There are two primary types of station pumps:
Trailer-Mounted Pumps: These pumps are mounted on a trailer for easy transportation to different job sites.
Truck-Mounted Static Pumps: These pumps are mounted on a truck chassis, providing mobility while maintaining the benefits of a stationary pump.
2. Preparing for Concrete Pumping
2.1 Site Assessment
Before setting up the station pump, conduct a thorough site assessment to identify potential challenges and ensure a safe working environment. Consider factors such as:
Accessibility: Ensure the pump and delivery pipeline can be safely and efficiently positioned.
Ground Conditions: Verify that the ground is stable enough to support the weight of the pump and equipment.
Obstacles: Identify and plan to navigate around obstacles such as power lines, trees, and existing structures.
2.2 Equipment Inspection
Inspect all components of the station pump system to ensure they are in good working condition. Check for any signs of wear or damage, and replace any defective parts. Key inspection points include:
Hoses and Pipes: Look for cracks, leaks, or blockages.
Pump Unit: Ensure the hydraulic system is functioning correctly and that all seals are intact.
Control Panel: Verify that all controls and indicators are working properly.
2.3 Concrete Mix Preparation
Prepare the concrete mix according to the project specifications. Ensure that the mix has the appropriate consistency and slump for pumping. A mix that is too dry may cause blockages, while a mix that is too wet may lead to segregation and reduced strength.
3. Setting Up the Station Pump
3.1 Positioning the Pump
Position the station pump on a stable, level surface close to the concrete supply. Ensure that the pump is securely anchored to prevent movement during operation.
3.2 Assembling the Delivery Pipeline
Assemble the delivery pipeline, connecting the pipes and hoses securely using clamps and couplings. Ensure that the pipeline is properly supported to prevent sagging and that all connections are airtight to avoid leaks.
3.3 Priming the Pump
Prime the pump by filling the hopper with a slurry mixture (typically water mixed with cement or a special priming agent). This helps to lubricate the pipeline and reduce friction, allowing the concrete to flow smoothly.
4. Operating the Station Pump
4.1 Starting the Pump
Turn on the pump using the control panel. Gradually increase the pump's pressure and flow rate to begin moving the slurry through the pipeline. Once the slurry has reached the end of the pipeline, you can start adding concrete to the hopper.
4.2 Monitoring the Pumping Process
Continuously monitor the pumping process to ensure smooth and efficient operation. Key aspects to monitor include:
Flow Rate: Adjust the flow rate as needed to match the project's requirements.
Pressure: Keep an eye on the pressure gauges to ensure the system is operating within safe limits.
Concrete Consistency: Regularly check the consistency of the concrete being pumped to ensure it meets the required specifications.
4.3 Handling Blockages
If a blockage occurs, immediately stop the pump and relieve the pressure in the pipeline. Locate the blockage and clear it using appropriate tools, such as a pipe cleaner or a reverse pumping technique. Once the blockage is cleared, re-prime the pump and resume operation.
4.4 Safety Precautions
Safety is paramount when operating a station pump concrete system. Follow these safety precautions to minimize risks:
Personal Protective Equipment (PPE): Ensure all personnel wear appropriate PPE, including hard hats, gloves, safety glasses, and high-visibility clothing.
Communication: Maintain clear communication between the pump operator, concrete supplier, and placement crew.
Emergency Procedures: Have a plan in place for dealing with emergencies, such as pump malfunctions or concrete spills.
5. Completing the Pumping Operation
5.1 Cleaning the Pump and Pipeline
Once the concrete pumping operation is complete, thoroughly clean the pump and delivery pipeline to prevent concrete from hardening inside the system. Follow these steps:
Flush with Water: Use water to flush out any remaining concrete from the hopper and pipeline.
Use Cleaning Balls: Insert cleaning balls into the pipeline to remove residual concrete and ensure a thorough cleaning.
Disassemble and Inspect: Disassemble the pipeline and inspect each component for cleanliness and any signs of wear or damage.
5.2 Maintenance and Storage
Perform routine maintenance on the station pump to keep it in optimal working condition. Key maintenance tasks include:
Lubrication: Regularly lubricate moving parts to prevent wear and tear.
Hydraulic System: Check the hydraulic fluid levels and replace the fluid as needed.
Inspection: Conduct regular inspections to identify and address any potential issues before they become major problems.
Store the pump and accessories in a clean, dry place to protect them from the elements and prolong their lifespan.
Using a station pump concrete system efficiently and safely requires careful planning, proper setup, and vigilant operation. By understanding the components and functions of the pump, preparing the site and equipment, and following best practices for operation and maintenance, you can ensure a successful concrete pumping operation.
Station pump concrete systems offer numerous advantages, including the ability to deliver concrete to hard-to-reach areas, increased efficiency, and reduced labor costs. By leveraging these benefits and adhering to safety protocols, construction professionals can achieve high-quality results and contribute to the overall success of their projects.
Whether you are working on a high-rise building, a bridge, or a large industrial facility, mastering the use of a station pump concrete system will enhance your capabilities and enable you to tackle complex construction challenges with confidence. Get your stationary concrete pump from Aimix.

Comments