The Importance of Regular Maintenance in Batching Plant Work
- aimixglobal5
- Oct 10, 2024
- 4 min read
Batching plants are essential components of the construction and concrete production industries. They are responsible for mixing raw materials, such as cement, aggregates, and water, to produce concrete that meets specific requirements for various projects. Given the demanding nature of batching plant work, regular maintenance is crucial to ensure optimal performance, minimize downtime, and extend the lifespan of the equipment. This article explores the importance of regular maintenance in batching plant work and outlines best practices for maintaining these vital systems.
The Role of Batching Plants in Construction
Batching plants serve as the backbone of concrete production. They provide the precise mixing and consistency required to meet the stringent standards of construction projects, whether for buildings, roads, bridges, or other infrastructure. The efficiency and reliability of batching plants directly impact the quality of the final product, making regular maintenance essential to maintaining high standards of performance.
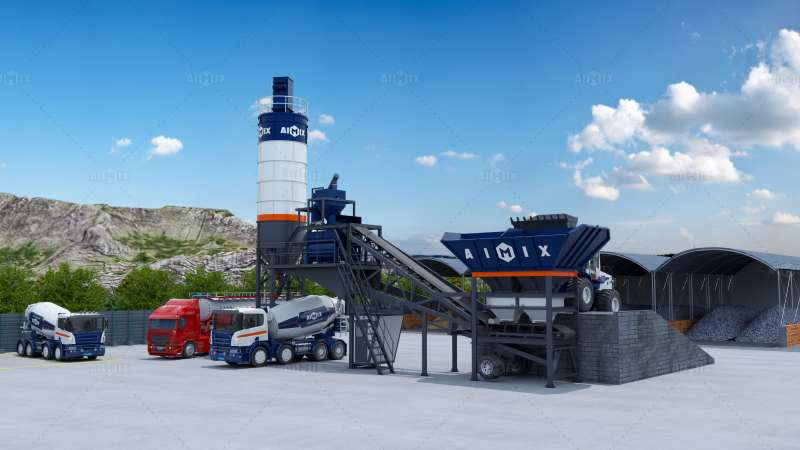
Benefits of Regular Maintenance
Enhanced Equipment Longevity
Regular maintenance plays a critical role in extending the lifespan of batching plant equipment. Like any complex machinery, batching plants are subject to wear and tear over time. Routine inspections, cleaning, lubrication, and replacement of worn-out parts can help prevent premature equipment failure and costly repairs. By investing in regular maintenance, companies can ensure their batching plants operate efficiently for many years.
Improved Efficiency and Productivity
A well-maintained batching plant operates more efficiently, resulting in higher productivity levels. Regular maintenance helps identify and rectify issues that could hinder the plant’s performance. For instance, worn-out components or misaligned parts can lead to reduced mixing efficiency, affecting the quality of the concrete produced. By ensuring that all equipment is functioning optimally, companies can maximize production rates and minimize delays.
Consistent Quality Control
Concrete quality is paramount in construction projects. Inconsistent mixing or variations in material proportions can lead to inferior concrete that fails to meet project specifications. Regular maintenance helps ensure that batching plants are calibrated correctly, and all components, such as weighing systems and mixers, are functioning as intended. This consistency is crucial for delivering high-quality concrete that meets industry standards.
Reduced Downtime and Costs
Unplanned downtime can be costly for businesses, leading to project delays and lost revenue. Regular maintenance helps identify potential problems before they escalate into major failures. By addressing minor issues during routine checks, companies can prevent costly breakdowns and the associated downtime that disrupts operations. Additionally, a well-maintained batching plant is less likely to require expensive repairs, ultimately saving money in the long run.
Increased Safety
Safety is a top priority in any industrial setting. Batching plants can pose various hazards if not maintained correctly, including equipment malfunctions and accidents caused by faulty machinery. Regular maintenance includes safety checks and inspections, ensuring that all safety features, such as emergency shut-off systems and safety guards, are functioning properly. A safe working environment protects employees and reduces the risk of accidents that can lead to injuries and legal liabilities.
Aimix is a professional batching plant manufacturer and supplier, has been in this industry for many years, and provides both quality plant equipment and professional services to make sure the batching plant works reliably. You can check Aimix company to know more details about batching plants.

Best Practices for Batching Plant Maintenance
To ensure the effectiveness of regular maintenance in batching plant work, companies should adopt the following best practices:
Create a Maintenance Schedule
Develop a comprehensive maintenance schedule that outlines routine inspections, cleaning, and repairs. This schedule should be based on manufacturer recommendations and the specific needs of the batching plant. Regularly reviewing and updating the schedule will help ensure that no critical maintenance tasks are overlooked.
Conduct Regular Inspections
Routine inspections are vital for identifying potential issues before they become significant problems. Operators and maintenance personnel should regularly inspect key components of the batching plant, including mixers, conveyors, weighing systems, and control panels. Look for signs of wear, corrosion, or misalignment, and address these issues promptly.
Keep Detailed Maintenance Records
Maintaining accurate records of all maintenance activities is essential for tracking the history of the batching plant’s performance. These records can help identify patterns or recurring issues, guiding future maintenance efforts. Additionally, detailed records provide valuable documentation for warranty claims and compliance with industry regulations.
Invest in Training and Education
Proper training for operators and maintenance personnel is crucial for effective maintenance practices. Regular training sessions should cover equipment operation, troubleshooting, and safety protocols. Well-trained staff will be more adept at identifying issues and ensuring that maintenance tasks are performed correctly.
Utilize Professional Services
While in-house maintenance is essential, companies may also benefit from utilizing professional maintenance services. External experts can provide specialized knowledge and experience, particularly for complex repairs or upgrades. Partnering with reputable service providers can enhance the overall maintenance program.
Conclusion
Regular maintenance is a critical aspect of batching plant work that significantly impacts equipment performance, product quality, and overall operational efficiency. By prioritizing maintenance activities, companies can extend the lifespan of their batching plants, reduce downtime, ensure consistent concrete quality, and enhance workplace safety. Implementing best practices for maintenance not only protects the investment in batching plant equipment but also contributes to the success of construction projects. In an industry where precision and reliability are paramount, investing in regular maintenance is not just a necessity but a strategic advantage.
Comments