How Concrete Batch Plant Manufacturers Are Adapting to Industry Trends
- aimixglobal5
- Dec 3, 2024
- 4 min read
The concrete batching industry is constantly evolving, influenced by technological advancements, environmental regulations, and shifts in market demand. As the construction industry faces increasing pressure to improve efficiency, sustainability, and quality control, concrete batch plant manufacturers are adapting their products and practices to meet these challenges. In this article, we will explore how concrete batch plant manufacturers are responding to current industry trends, including automation, sustainability, cost-efficiency, and customization.

1. Embracing Automation for Increased Efficiency
One of the most significant trends in the construction and manufacturing sectors is the shift toward automation. Concrete batch plant manufacturers are integrating advanced automation technologies into their systems to enhance operational efficiency and reduce human error. Automated systems allow for precise control over the mixing process, ensuring consistent concrete quality. Automation also helps optimize the use of raw materials, reducing waste and ensuring that every batch meets the required specifications.
For example, many modern batch plants now feature integrated control systems that can monitor and adjust the mixing process in real time. These systems can track variables such as material flow, water content, and mix ratios, allowing for precise adjustments and reducing the need for manual intervention. This not only improves the quality of the final product but also boosts the overall speed and efficiency of production, leading to faster project completion times.
Manufacturers are also incorporating remote monitoring and control features, allowing operators to manage and troubleshoot plant operations from anywhere. This level of automation and control reduces downtime, lowers labor costs, and ensures smoother operations across construction sites.
2. Focusing on Sustainability
As environmental concerns continue to grow, concrete batch plant manufacturers are increasingly focusing on sustainability in their designs and operations. Sustainable practices are becoming a major consideration for construction companies, both in terms of reducing their carbon footprint and complying with stricter regulations.
Batch plant manufacturers are adopting technologies that minimize energy consumption, reduce emissions, and recycle waste materials. For example, some batch plants are designed to incorporate energy-efficient motors, heat recovery systems, and optimized mixing processes that reduce the overall energy consumption. In addition, manufacturers are using greener materials, such as recyclable steel and eco-friendly coatings, to reduce the environmental impact of production.
One of the most important sustainability trends is the development of concrete recycling systems. Many modern batch plants now feature built-in systems to recycle excess concrete, preventing waste from being discarded into landfills. These systems can recycle concrete slurry and leftover mixed materials, allowing for their reuse in future batches. This not only reduces environmental impact but also cuts down on material costs for construction companies.
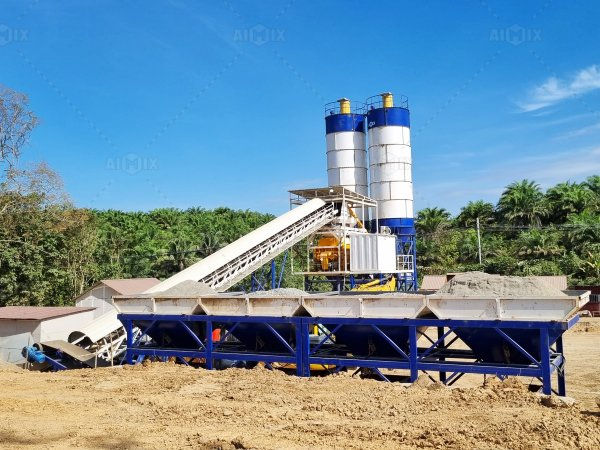
3. Customization to Meet Specific Project Needs
Every construction project is unique, requiring tailored concrete solutions. To meet this demand, concrete batch plant manufacturers are offering more customization options for their clients. Whether it’s for a large-scale infrastructure project or a small commercial development, manufacturers are now able to design batch plants that meet the specific requirements of a project.
For instance, manufacturers are providing various plant configurations, such as stationary, mobile, and modular plants, to offer greater flexibility in meeting the logistical needs of a project. Mobile concrete plants are particularly popular in projects where the site location changes frequently, offering the convenience of easy transportation and quick setup. Modular plants, on the other hand, allow for easy expansion and reconfiguration as the needs of a project evolve.
Additionally, batch plant manufacturers are offering customizable mix designs to meet specific concrete quality standards. Whether it’s for high-strength concrete, self-compacting concrete, or specialized mixes for particular environmental conditions, manufacturers are tailoring their equipment to ensure that each batch plant delivers the right mix for the project at hand.
4. Improving Cost-Effectiveness and Value
As competition in the construction industry intensifies, cost-effectiveness remains a priority for both contractors and concrete batch plant manufacturers. In response, manufacturers are working to reduce the operational and upfront costs associated with batch plants. By focusing on efficient design, streamlined production processes, and high-quality materials, manufacturers can offer more affordable solutions without compromising performance.
For example, batch plant manufacturers are designing more compact and energy-efficient models that reduce both initial investment costs and long-term operating expenses. These models require less space and can be set up more quickly, reducing the overall costs associated with construction site preparation. Additionally, the use of advanced automation and optimized processes reduces labor requirements, further cutting down on operational costs.
Manufacturers are also offering cost-saving solutions through maintenance packages and extended warranties. Proactive maintenance and early identification of issues help prevent costly repairs and downtime, ensuring that the plant continues to operate efficiently throughout its lifespan.
5. Adapting to Digitalization and Data-Driven Operations
Another key trend in the concrete batching industry is the rise of digitalization. Manufacturers are incorporating advanced data analytics and Internet of Things (IoT) technologies into their systems to improve decision-making, optimize plant performance, and enhance customer service.
For instance, many modern batch plants come equipped with IoT sensors that provide real-time data on plant performance, material usage, and environmental conditions. This data can be used to predict maintenance needs, optimize material usage, and reduce waste. Batch plant manufacturers are using this data not only to improve plant operations but also to offer value-added services to customers, such as performance analysis and remote diagnostics.
The integration of digital tools also allows construction companies to have more control over their projects. With cloud-based systems, plant operators can access production data from anywhere, enabling faster decision-making and greater transparency throughout the project.
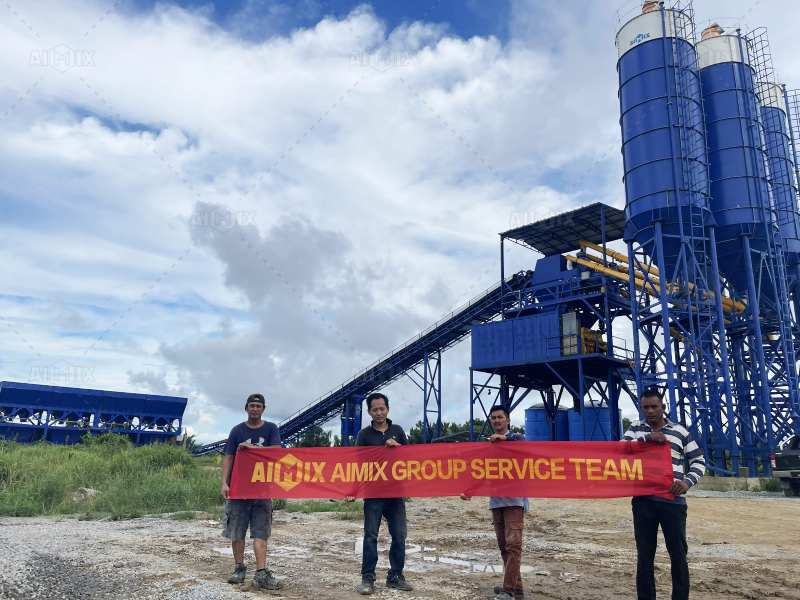
6. Meeting Global Standards and Regulations
As regulations regarding concrete production become more stringent, batch plant manufacturers are adapting by designing equipment that meets or exceeds local and international standards. Whether it’s for environmental compliance, safety regulations, or quality assurance, manufacturers are ensuring that their plants adhere to the latest industry guidelines.
This includes complying with standards for emissions, noise levels, and dust control, as well as ensuring that the plants are equipped with the necessary safety features for workers. By staying ahead of regulatory changes, manufacturers help their clients avoid penalties and ensure smoother operations throughout the construction process.
Conclusion
Concrete batch plant manufacturers are constantly adapting to the evolving demands of the construction industry. By embracing automation, sustainability, and customization, they are providing businesses with more efficient, eco-friendly, and cost-effective solutions. As technological advancements continue to shape the industry, manufacturers will continue to innovate, offering new features that enhance performance, reduce costs, and meet the specific needs of modern construction projects. By staying attuned to these trends, manufacturers are helping companies improve their operations and achieve long-term success.
Comments