How to Optimize Production at Your Ready Mix Concrete Plant
- aimixglobal5
- Sep 30, 2024
- 3 min read
Ready mix concrete plants are essential in modern construction, providing a consistent supply of concrete tailored to specific project needs. Optimizing production at your ready mix concrete plant is crucial for enhancing efficiency, reducing costs, and ensuring high-quality output. This article outlines key strategies for optimizing production processes, improving workflow, and maximizing the effectiveness of your ready mix concrete plant operations.
1. Streamline Operations with Technology
Incorporating advanced technology can significantly enhance production efficiency. Here are some technological solutions to consider:
Batching Control Systems: Invest in a robust batching control system that automates the weighing and mixing processes. These systems ensure accuracy and consistency in mix ratios, reducing material waste and improving product quality.
Real-Time Monitoring: Implement real-time monitoring systems that track production metrics, including batch times, material usage, and output rates. This data can help you identify bottlenecks in the production process and make informed decisions for optimization.
Mobile Applications: Use mobile applications to manage orders and deliveries efficiently. This can improve communication between the plant and delivery teams, ensuring timely dispatch and reducing idle time for trucks.

2. Focus on Quality Control
Quality control is essential for maintaining the integrity of your concrete products. Optimizing quality can lead to fewer reworks and increased customer satisfaction:
Standardized Mix Designs: Develop standardized mix designs based on specific project requirements. This ensures consistency in the concrete produced, leading to better performance in the field.
Regular Testing: Conduct routine testing of raw materials and finished products. Regular slump tests, compressive strength tests, and aggregate grading checks can help you catch any quality issues early and maintain high standards.
Training for Operators: Ensure that your operators are well-trained in quality control procedures. Regular training sessions can help them recognize potential quality issues and adhere to best practices in mixing and handling concrete.
3. Efficient Material Management
Efficient management of raw materials is vital for optimizing production:
Inventory Management: Implement an effective inventory management system to track the levels of cement, aggregates, and admixtures. This can help prevent shortages and ensure you have the necessary materials on hand for production.
Supplier Relationships: Develop strong relationships with suppliers to ensure timely deliveries of high-quality materials. Consider establishing agreements that allow for just-in-time deliveries, reducing the need for extensive storage and minimizing waste.
Reduce Material Waste: Analyze your material usage to identify opportunities for reducing waste. This can include optimizing mix designs to use less material without compromising quality or reusing excess concrete when possible.
As a reliable concrete plant supplier, Aimix has much experience in offering quality batching plants to suit different construction needs.
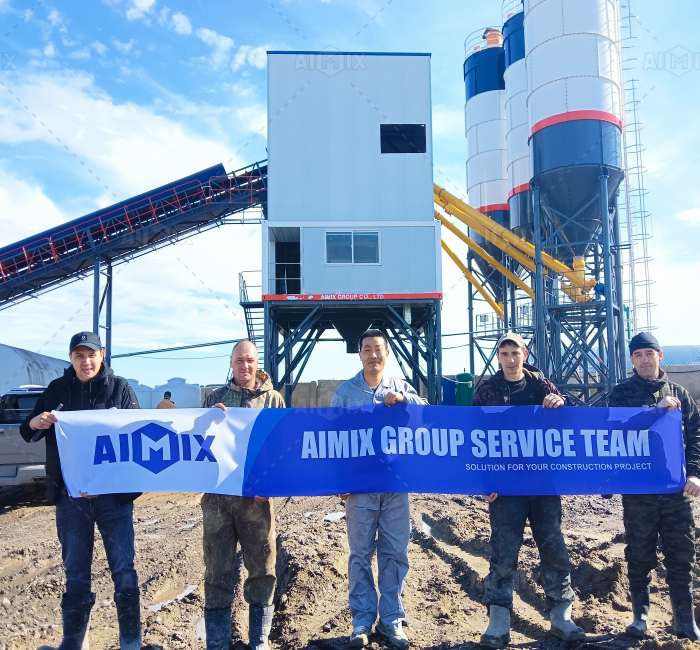
4. Optimize Workflow and Layout
The layout and workflow of your ready mix concrete plant can significantly impact production efficiency:
Plant Layout: Design your plant layout for optimal flow of materials and personnel. Minimize the distance between raw material storage, batching, mixing, and dispatch areas to reduce transportation time.
Organized Workstations: Ensure that workstations are well-organized and equipped with necessary tools and equipment. This reduces downtime as operators can quickly access what they need.
Clear Communication Channels: Establish clear communication channels between different teams in the plant. Regular meetings and updates can help ensure that everyone is aligned and aware of production goals.
5. Regular Maintenance and Inspections
Routine maintenance of equipment is critical for avoiding downtime and ensuring smooth operations:
Scheduled Maintenance: Create a maintenance schedule for all equipment, including mixers, conveyors, and batching systems. Regular inspections can help identify potential issues before they lead to breakdowns.
Quick Repairs: Keep spare parts on hand for critical components to facilitate quick repairs. Minimizing downtime is crucial for maintaining production schedules.
Operator Responsibility: Encourage operators to conduct daily checks on equipment before starting production. This proactive approach can help catch minor issues before they escalate.

6. Employee Training and Engagement
Investing in your workforce is key to optimizing production:
Ongoing Training: Provide regular training opportunities for employees on best practices, safety protocols, and new technologies. A well-trained workforce is more efficient and productive.
Employee Engagement: Foster an environment where employees feel valued and encouraged to share ideas for improvement. Engaging your workforce can lead to innovative solutions that enhance production processes.
Performance Metrics: Implement performance metrics to track employee contributions to production goals. Recognizing and rewarding high performers can boost morale and motivate the team to work towards optimization.
Conclusion
Optimizing production at your ready mix concrete plant involves a multifaceted approach that includes leveraging technology, focusing on quality control, managing materials efficiently, optimizing workflow, maintaining equipment, and investing in employee training. By implementing these strategies, you can enhance operational efficiency, reduce costs, and ensure high-quality concrete products that meet customer demands. Continuous improvement should be a core focus, allowing your plant to adapt and thrive in a competitive market.
Comments